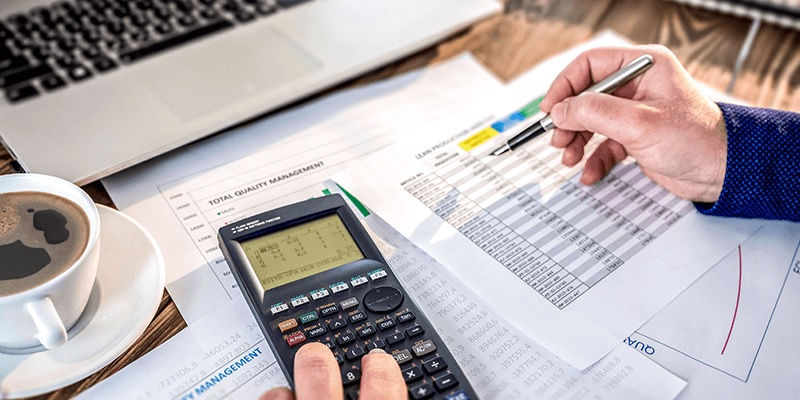
Bluestreak
Reading Time: 3 minutes
Despite technical advances, there is a failure to reduce production costs.
In reality, productivity in manufacturing is actually declining. Labor productivity dropped by nearly 1% in the first quarter of 2020, resulting in a 2.2% decrease in output. Combined with rising labor costs, growing material costs, and increased customer pressure to lower prices, it has reduced the already-thin profit margins for manufacturers.
A quality control plan and quality control system are now more important than ever to eliminate wasted materials, underperforming products or product defects, and lost opportunity costs.
But why aren’t more manufacturers taking proactive steps to reduce their production costs? Manufacturers today are enduring turbulent times that will shape the industry for decades to come. As a result, manufacturers became very focused on bottom-line margins and maintaining revenue during times of fierce competition and price cuts. This makes them skeptical of any new technologies or processes that don't have quantifiable and immediate ROI, and many fear technology trials are expensive science projects with no proven outcome. Here are some other reasons:
1. They Don’t Want to Take the Time to Retool
Retooling can be expensive and time-consuming. Machines that constantly break down or need maintenance only add to productivity declines and increase production cost. Many manufacturers don’t want to take the time to replace equipment. Likewise, they don’t want to stop work on the shop floor to learn new software or processes.
Instead of fixing the problems, they’ll live with downtime from older tech or machinery. After a while, they’ll learn to “accept” quality deficiencies, despite the significant negative impact of downtime on production cost.
2. They Fear That Workers Can’t Handle the Changes
Many of the most experienced and skilled workers in manufacturing are aging. Some manufacturers fear that employees used to doing a job a certain way for years (maybe decades) will be unwilling or unable to learn new skills. Forcing skilled workers to do a job differently may cause them to quit.
In turn, if workers are not convinced that changes will lead to positive results, like increased productivity or lower production cost, they’re not likely to embrace the change. In worst-case scenarios, some may even actively fight the changes.
3. They’re Not Tracking the Cost of Quality
Most manufacturers say that they don’t know their cost of quality, despite the effect it has on profits. If they’re not tracking the cost of quality—and the impact of poor quality—it’s difficult to recognize the problem and do something about it.
Industry statistics put the cost of quality at 10-25% of revenue, with some manufacturers spending twice that amount. Without the correct data, they may be unable to find the problem and manage the process.
4. They Think That the Only Solution Is an Expensive ERP System
Manufacturers believe that the solution is an enterprise resource planning (ERP) system, but the cost is too high. Actually, this system is overkill for their needs in most cases and is therefore difficult to justify.
There’s no reason to pay for features that you aren’t going to use. Bluestreak MES/QMS software provides the functionality that most manufacturers need at a fraction of the cost of a customized ERP solution.
Some companies make the mistake of using a full-blown ERP system that isn’t doing what they need on the shop floor. This type of system records transactional data and reports it, which doesn’t meet the needs of the production manager and plant supervisor, who need software that records every production step on the floor in real-time and ties their QMS directly to the operators and equipment. If you already have an ERP system in place, Bluestreak’s manufacturing execution system (MES) and quality management system (QMS) can be easily integrated to give you a complete end-to-end picture of what’s happening in your manufacturing facility.
The Bottom Line
It’s often easier to maintain the status quo than to make changes that can improve productivity and reduce operational costs. The opportunity is there if leaders are willing to take it. Improvement starts with tracking data through Bluestreak and monetizing the value of the process.
A centralized tracking platform, such as Bluestreak MES/QMS software, simplifies each step for all levels of participants to do their part. Whether workers on the floor or supervisors and management, having visibility throughout the process keeps a finger on the pulse of production costs from start to finish.
If you’re ready to leave manual, time-consuming service-based manufacturing tasks in the past, drastically reduce your scrap and rework percentage, gain visibility of your production floor processes, and build better relationships with your customers, contact us for a free consultation today!
About Bluestreak™:
Bluestreak™ is a powerful Manufacturing Execution System (MES) and a fully integrated Quality Management System (QMS), designed for the manufacturing environment and service-based manufacturing companies ( metal-treating/powder-coating, plating, heat-treating, forging, and metal-finishing), businesses that receive customers’ parts, perform a process (service) on them, and send those parts back to the customer). Companies need MES software tailored to specific functionality and workflow needs such as industry-specific specifications management, intuitive scheduling control for both staff and machinery maintenance, and the ability to manage work orders and track real-time data. If different work centers on the production floor aren’t “speaking” to each other via the MES, the data loses value and becomes disjointed or lost in disparate silos.
Bluestreak | Bright AM™ is an MES + QMS software solution specifically designed to manage and optimize the unique requirements of Additive Manufacturing’s production of parts and powder inventory usage.
Comments