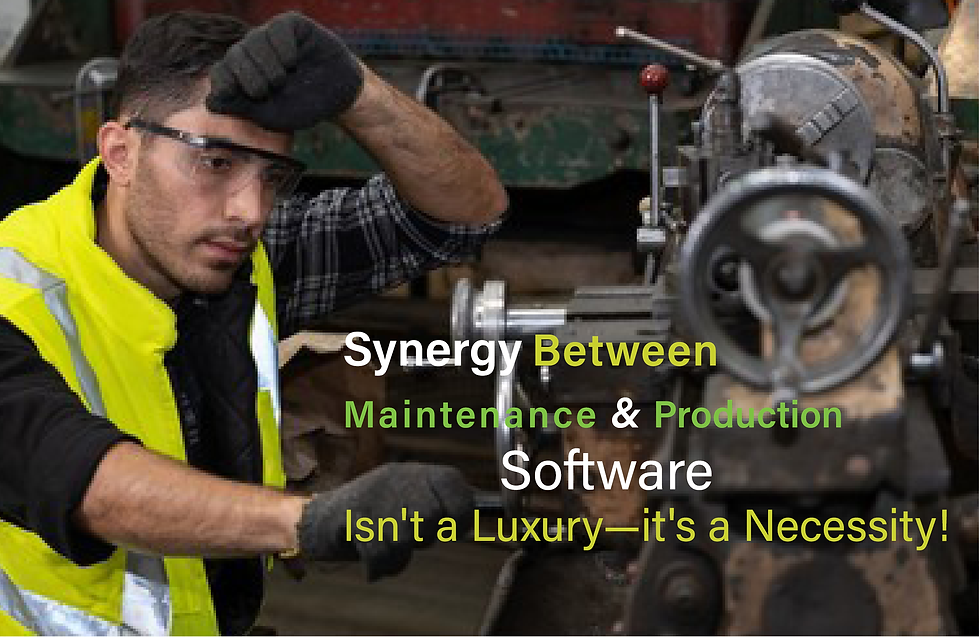
Bluestreak Reading Time: 5 minutes
Unifying Maintenance and Production Software: The Key to Seamless Operations for Heat Treaters
Heat treating, a cornerstone of modern metallurgy, plays a vital role in enhancing the properties of metals. It's a nuanced, precision-driven process where metals are heated and cooled under strictly controlled conditions to achieve desired characteristics. The slightest deviation or error can be costly both in terms of product quality and operational efficiency. This magnifies the importance of maintaining the machinery and equipment in optimal condition. And yet, in many operations, maintenance exists in a silo, separate from the rhythm and demands of the production floor. This needs to change. Here's why a harmonious synergy between maintenance and production is the key to seamless operations for Heat Treaters.
Optimizing Operational Uptime: In heat treating, even brief interruptions can jeopardize an entire batch of work. Whether it's a delay in reaching the requisite temperature or an unexpected shutdown, any deviation can mean significant material wastage. Unplanned maintenance activities, unfortunately, often lead to such interruptions. By harmonizing maintenance schedules with production timelines, equipment servicing or replacements can be done during planned downtimes or periods of lower activity. This not only maximizes uptime but also prevents costly disruptions. Guaranteeing Quality and Consistency: The reputation of a heat treater hinges on the quality of its output. Metals that have not been treated under the right conditions may not exhibit the desired properties and can fail when used in real-world applications. Well-maintained equipment ensures that the production process remains consistent. When maintenance works in tandem with production, it ensures that the equipment is always in its prime operational state, maintaining a uniform quality in the output. Safety First and Always: Heat treating involves dealing with extreme temperatures, and often, potentially hazardous conditions. Equipment that isn't properly maintained can become a safety risk. A small leak, a minor electrical fault, or a calibration error can lead to serious accidents on the production floor. Keeping maintenance in step with production ensures that equipment health is regularly checked, and any potential safety hazards are addressed immediately. Cost Efficiency at its Best: Think of a scenario where a critical furnace component fails during peak production hours. The immediate costs involve the halted production, potential damage to the material inside, and emergency repair or replacement expenses. The indirect costs include delayed deliveries, overtime wages, and potential loss of business credibility. By ensuring that maintenance is synchronized with production, such emergency scenarios can be drastically reduced. Preventive and predictive maintenance, aligned with production demands, leads to significant cost savings in the long run.
Empowering Data-Driven Decisions: Modern heat treating operations are increasingly reliant on data analytics for decision-making. By bringing maintenance into the fold, a richer, more comprehensive dataset emerges. This data can offer insights into the correlation between equipment health and product quality, the impact of maintenance activities on production efficiency, and more. Decisions about equipment upgrades, process optimizations, and production scheduling become more informed and precise. The Feedback Loop: A cohesive approach between maintenance and production paves the way for a continuous feedback loop. Production staff, with their hands-on experience, can quickly notice anomalies or sub-optimal performance in equipment. When such observations are promptly relayed to the maintenance team, immediate action can be taken. This feedback mechanism prevents minor issues from snowballing into major problems. Bridging the Communication Gap
Across industries, maintenance is typically considered a service department rather than an integrated part of production and operations. This is a mistake because it can lead to communication barriers. To improve uptime and, therefore, production, heat treaters should instead, set up their maintenance teams to function in a proactive vs. reactive way. In an integrated system, the dialogue is ongoing. Maintenance knows of production priorities, and production is aware of maintenance schedules. This fosters a collaborative environment where both teams work towards the common goal of operational excellence. The Competitive Edge The complex and precision-driven world of heat treating underscores the importance of every cog in the machine working flawlessly. Maintenance, often seen as the backstage crew, plays a starring role in ensuring the show goes on without a hitch. By integrating maintenance activities with the rhythm of the production floor, heat treaters can elevate their operations to new heights, ensuring quality, safety, and efficiency at every step. It's not just a strategic move; it's the future of efficient and effective heat treatment.
An integrated software solution like Bluestreak's iMaintain™, and Production Pathway™ helps with fine-tuning the teaming between maintenance and production. Contact us for a complimentary consultation.
About Bluestreak™:
Bluestreak™ is a powerful Manufacturing Execution System (MES) and a fully integrated Quality Management System (QMS), designed for the manufacturing environment and service-based manufacturing companies ( metal-treating/powder-coating, plating, heat-treating, forging, and metal-finishing), businesses that receive customers’ parts, perform a process/ service on them, and send those parts back to the customer). Companies need MES software tailored to specific functionality and workflow needs such as industry-specific specifications management, intuitive scheduling control for both staff and machinery maintenance, and the ability to manage work orders and track real-time data. If different work centers on the production floor aren’t “speaking” to each other via the MES, the data loses value and becomes disjointed or lost in disparate silos.
Bluestreak | Bright AM™ is an MES + QMS software solution specifically designed to manage and optimize the unique requirements of Additive Manufacturing’s production of parts and powder inventory usage.
Comments