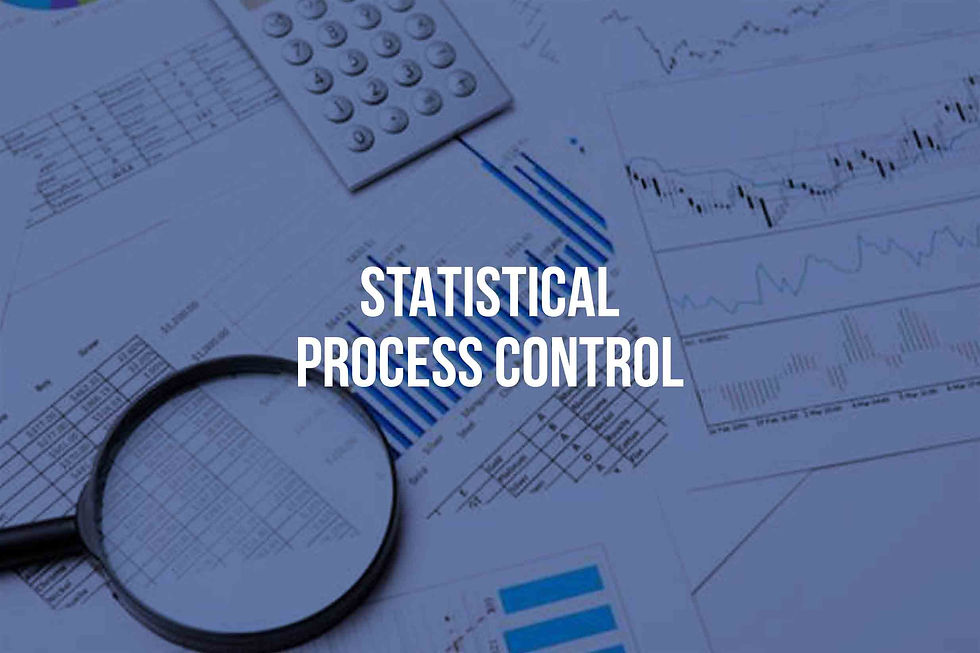
Bluestreak Reading Time: 7 minutes
The Key Benefits of Statistical Process Control (SPC)
The true potential of SPC (Statistical Process Control) unfolds beyond the shop floor, revealing its utmost success when engineers, quality professionals, and managers utilize the data to implement extensive, high-level improvements throughout their operations. In these instances, control charts become less prevalent. Although data is initially collected on the shop floor to regulate processes, its value transcends as it is repurposed and aggregated across various processes, products, and even plants. This transformation yields profound insights, surpassing the capabilities of control charts or older software technologies, which quality professionals could never achieve.
Regrettably, a prevalent mistake made by organizations is restricting SPC solely to the shop floor. The key lies in intelligently leveraging the data and information generated by the SPC system to enhance business performance across the entire enterprise. The key benefits of Statistical Process Control are multi-faceted, as SPC not only substantially reduces overall costs and improves efficiencies at the plant level but also empowers organizations to evaluate quality throughout all their operations. Consequently, this enables the identification and prioritization of strategic improvements, ultimately leading to a significant competitive advantage.
1. Providing Real-time Operator Feedback and Delivering Actionable Information Immediately.
The process begins at the shop floor, where operators make use of control charts. After periodic data collection, operators receive feedback as the collected data is converted into plots on a control chart, visually representing their data. Operators often manage multiple control charts, each dedicated to various product features and characteristics, such as width, height, length, diameter, and specific parameters like spindle speeds, temperatures, and dwell time.
Similar to how healthcare providers interpret an electrocardiogram (EKG) to measure the electrical activity of heartbeats and identify abnormal spikes or lapses in rhythm indicating potential health issues, control chart usage functions similarly. These charts provide a means for operators to gauge the stability of their machinery. By promptly alerting them to abnormal situations, control charts help identify potential issues that could negatively impact the quality of the products they manufacture.
Let's consider an example: imagine an operator working in a factory that produces fan blades. In this scenario, the weight of the blades holds critical importance both to the operator and the company. If the weight falls below the specified amount, it can lead to dissatisfaction among regulatory agencies and consumers. On the other hand, excessive weights beyond the package specifications are deemed as "giveaways," resulting in increased manufacturing costs and reduced profits. Hence, achieving the right balance in weights is essential - not too heavy, not too light - requiring meticulous control over the machines responsible for making the bars.
Whenever the weights deviate too low, spike too high, or undergo sudden changes, this crucial information is immediately communicated to the operator. Thanks to the real-time availability of such data, operators can promptly take action, preventing potential larger issues and costs in the future.
2. Improved Problem-Solving Capabilities
Instant feedback derived from control charts provides operators with valuable insights into the performance of a production line, ensuring that weights and other critical characteristics align with historical data. However, the data holds even more valuable information. By analyzing specific plot point patterns, operators and quality managers can identify the nature and source of encountered issues, thus bolstering problem-solving abilities and fostering a deeper understanding of process behavior.
For instance, if a plot point suddenly surpasses a control limit, operators recognize that an atypical event has occurred, prompting them to take immediate action to rectify the change. On the other hand, steadily increasing or decreasing plot points over time indicate a gradual process change, hinting at a potentially different underlying issue. These distinct patterns and events highlighted by control charts serve as clues that empower operators, engineers, and quality professionals to effectively resolve problems.
In the aerospace manufacturing industry, imagine a company that produces intricate components for aircraft engines, situated in a region known for its aerospace expertise. They supply parts to a prominent aircraft manufacturer. However, a major issue has arisen - the components they deliver are causing disruptions in the aircraft assembly process for their customer. These disruptions have escalated to the point where the aircraft manufacturer is incurring substantial costs due to extended downtime.
To address these quality issues and ensure the production of flawless components, the aerospace company decides to implement SPC and control charts in their CNC machining centers - the final crucial step in manufacturing these aerospace parts. Before the deployment, their skilled operators undergo comprehensive training in SPC techniques.
During one shift, a seasoned operator is running a CNC machining center when he notices something intriguing. He carefully monitors critical parameters related to the component's dimensions and plots the data point on the control chart. To his surprise, the data point falls below the control limit, indicating a dimension significantly lower than expected.
Being attentive and proactive, the operator raises his concerns. "This is unusual. If the component's dimension is that low, we might expect issues during assembly, but there aren't any apparent problems so far," he remarks.
Encouraged to follow his instincts, the operator decides to conduct a more thorough inspection of the CNC machine. He sets aside his tools and takes a closer look, even peering underneath the machine. To his astonishment, he discovers a tiny obstruction - a jam that was not easily visible from a distance. This seemingly insignificant jam is, in fact, causing a significant reduction in the performance of a critical feature of the aerospace component.
Thanks to the insights gained from the control chart, the operator promptly rectifies the issue, ensuring that the subsequent components meet the desired specifications. By leveraging SPC techniques and operator vigilance, the aerospace company successfully maintains the high quality of its components, minimizing disruptions for its valued customer and sustaining its reputation for precision engineering in the aerospace industry.
3. Ensuring Product Consistency in the Present and Future
Ensuring product uniformity stands as a crucial priority for manufacturers, yielding not only cost savings by preventing scrap, rework, and overfill but also guaranteeing unwavering customer satisfaction and compliance with regulatory standards.
A prominent example comes from a major manufacturer of automobile transmissions, which encountered an unexpected surge in warranty claims for transmission issues approximately two years after launching a new vehicle model. To resolve this concern, the quality team initiated a thorough investigation and discovered that the transmissions were being produced in two different locations. Although both plants adhered to identical quality guidelines, they utilized distinct machinery for the manufacturing process.
Upon examining transmissions and their components from each location, a vital insight emerged: all transmissions from both Plant A and Plant B fell within the specified limits. However, a notable difference arose when analyzing critical dimensions. Transmissions from Plant A closely matched engineering targets with minimal variation, while those from Plant B exhibited more significant variability despite remaining within specification limits. Remarkably, neither plant had any out-of-specification parts in their transmissions.
Despite meeting the prescribed specifications, Plant B faced considerably higher warranty claims compared to Plant A. This discrepancy in warranty claims could be attributed to the varying levels of dimension variation in each plant. Plant A consistently produced transmissions with parts closely aligned to ideal targets, enhancing reliability, while Plant B's transmissions displayed greater variability.
This real-life case highlights the importance of product uniformity extending beyond mere compliance with specifications. Even when parts fall within the designated limits, variations in critical dimensions can profoundly impact performance and long-term reliability. For manufacturers, upholding consistent product quality, particularly concerning critical dimensions, proves crucial in satisfying customers and minimizing warranty-related costs. Employing techniques and control charts becomes invaluable in identifying and addressing such variations, enabling the creation of uniform and dependable products throughout the production process.
4. Lower Your Costs of Quality – Even When Nothing is Out of Spec In the competitive aerospace industry, achieving superior quality standards while maintaining cost efficiency is a perpetual challenge for manufacturers. One such aerospace company, with a commitment to excellence, successfully implemented innovative measures to lower its Costs of Quality (CoQ), even in instances where nothing was out of specification.
This manufacturer recognized that CoQ encompassed not only the expenses related to addressing non-conformances, rework, and warranty claims but also the hidden costs associated with inefficiencies, delays, and lost opportunities due to minor variations in their production processes. To address this challenge, they turned to the principles of SPC and continuous improvement.
SPC enabled the aerospace manufacturer to monitor their manufacturing processes proactively, gathering real-time data on critical parameters through control charts and other analytical tools. This allowed them to identify trends, variations, and potential issues before they escalated into costly problems.
Interestingly, even when their products were well within specification limits, the manufacturer found opportunities to optimize their processes further. By reducing process variation and maintaining tighter control around target values, they observed a considerable reduction in CoQ.
One significant area of improvement was their assembly process for aircraft components. Although parts were meeting the required specifications, minor variations were leading to inconsistencies in fit and performance during the final assembly. By employing SPC techniques to minimize variability, they enhanced the compatibility of their components, leading to smoother assembly operations and a reduction in subsequent warranty claims.
Moreover, their quality teams collaborated with process engineers to analyze historical data, aiming to uncover potential process improvements. This data-driven approach identified subtle inefficiencies and variations that might have otherwise gone unnoticed. By addressing these issues, they mitigated the risk of future quality problems and avoided costly rework or scrap.
Furthermore, the aerospace manufacturer emphasized continuous training and engagement of their workforce in the principles of SPC and Lean Manufacturing. Employees were encouraged to contribute ideas for process optimization, leading to a culture of continuous improvement throughout the organization.
As a result of their proactive approach and dedication to quality, this aerospace manufacturer experienced a significant decline in CoQ, contributing to increased profitability and customer satisfaction. Their commitment to lowering CoQ, even when nothing was out of specification, fostered a culture of excellence and operational efficiency, positioning them as a leading player in the aerospace industry. Through the successful integration of SPC and continuous improvement principles, they continue to thrive by delivering top-notch products while maximizing cost-effectiveness and maintaining a competitive edge.
5. Identify Areas for Enhancement Throughout the Entire Organization. The spirits company discussed above made a significant discovery: their management team was unaware of the extent to which they were overfilling their products and the potential cost savings they could achieve. The information remained hidden because they believed that since everything was within specification limits, no further improvements were possible. However, the data were available; they simply hadn't been thoroughly examined.
This scenario is quite common. Quality teams, engineers, and managers often overlook shop floor quality data unless a specific problem is indicated. By limiting the use of SPC solely to the shop floor, organizations miss out on the potential for substantial improvements, just like the spirits company experienced. Valuable insights lie within the data collected on the shop floor, but it is essential for organizations to consistently review and analyze this data to unlock significant gains in both quality and cost.
One of the key advantages of using SPC is that it enables companies to unearth previously unknown information. Moreover, when they aggregate the data across multiple production lines, whether managed by plant floor managers or corporate quality professionals, they can precisely pinpoint and prioritize opportunities for improvement across the entire operations.
By taking a holistic approach to data analysis and actively leveraging SPC throughout the organization, companies can identify the hidden potential for cost savings, quality enhancement, and operational efficiency. This proactive use of data empowers organizations to make well-informed decisions, leading to substantial improvements and maximizing their overall success.
By aggregating and consolidating data in this manner, companies transcend the scope of comparing product-to-product and line-to-line; they also extend their analysis to encompass plant-to-plant comparisons. When implementing SPC, shop floor quality data is collected for critical characteristics throughout the company. In smart manufacturing facilities, this data is efficiently stored in a comprehensive database, comprising information from each quality check on every production line, for each product code, within each facility across the entire manufacturer's operation.
In conclusion, with this wealth of data at our disposal, quality professionals, Six Sigma teams, and engineers have the opportunity to extract valuable insights regarding overall operations. These data paint a broader picture of quality across the enterprise, leading to extraordinary results. Analyzing this comprehensive dataset enables organizations to identify opportunities for improvement, pinpoint areas of excellence, and make informed decisions to enhance their overall operational efficiency and product quality.
About Bluestreak™:
Bluestreak™ is a powerful Manufacturing Execution System (MES) and a fully integrated Quality Management System (QMS), designed for the manufacturing environment and service-based manufacturing companies ( metal-treating/powder-coating, plating, heat-treating, forging, and metal-finishing), businesses that receive customers’ parts, perform a process (service) on them, and send those parts back to the customer). Companies need MES software tailored to specific functionality and workflow needs such as industry-specific specifications management, intuitive scheduling control for both staff and machinery maintenance, and the ability to manage work orders and track real-time data. If different work centers on the production floor aren’t “speaking” to each other via the MES, the data loses value and becomes disjointed or lost in disparate silos.
Bluestreak | Bright AM™ is an MES + QMS software solution specifically designed to manage and optimize the unique requirements of Additive Manufacturing’s production of parts and powder inventory usage.
Comments