
Bluestreak™ Reading Time: 7 minutes
su•per•fi•ci•al•i•ty (Part Two)
Simplified QMS Software can Lead to Inadequate Outcomes
with Notable Downsides.
Inadequate Coverage
Oversimplification of processes to reduce clicks and speed up workflow can lead to quality gaps.
The presumption that processes are always performed correctly without rigorous verification or oversight can result in systemic failures and product non-conformities. Major issues arise when a simplified QMS does not incorporate comprehensive checks and balances to verify that each step of the manufacturing process is executed correctly. For instance, in the majority of part manufacturing, the assumption that machines are always calibrated correctly could lead to the production of parts that do not meet tolerance specifications. Over time, this can result in increased failures in the final product and not only impacts product reliability but also safety.
Moreover, assuming that production steps are always executed accurately can bypass critical control points meant to catch errors before they propagate through the production line. For example, if a metal stamping process is presumed to be flawless, defects like improper material thickness or incorrect die alignment might not be identified promptly. These defects, if unchecked, can lead to large batches of non-compliant products, necessitating costly recalls and rework and potentially damaging the manufacturer's reputation.
Manufacturing processes can drift due to changes in raw materials, environmental conditions, or machine wear. A robust QMS would typically include protocols for regular process review and adjustment. Without these, a manufacturer may continue to operate under the false belief that its processes are stable, potentially leading to significant quality deviations, failure to meet customer specifications, external audit findings, loss of new contracts, etc.
Lacks Depth and Breadth
Oversimplifying can often be insufficient to meet the nuanced and specific compliance needs of customer requirements due to its reliance on generic templates and a one-size-fits-all approach.
Such software typically provides basic frameworks and templates designed to cover a broad spectrum of industries and processes. However, this generality fails to address the unique challenges and specific standards that are required in different sectors of manufacturing.
In the aerospace manufacturing sector, where compliance with stringent standards like AS9100 is required, generic QMS templates might not include detailed workflows or documentation protocols that align with aerospace-specific regulations, such as those related to traceability and part validation. This oversight can lead to gaps in compliance and the inability to provide evidence during audits that all specific regulatory requirements are being met and leave manufacturers vulnerable to unforeseen problems that could have been mitigated with more robust, industry-specific QMS tools. You cannot cut corners if you want to be known for high quality and compliance.
Risk Management Failures
Risk identification and assessment fail to capture potential risks, leading to non-conformances and bottlenecks.
When QMS software does not provide real-time tracking and analysis, it fails to capture immediate data on process variations, equipment malfunctions, or deviations from standard operating procedures. For instance, in an assembly line for electronic devices, if the soldering temperature drifts outside the optimal range, a sophisticated QMS would detect this anomaly instantly and trigger alerts. However, a simplistic system might miss this deviation, resulting in a batch of products with poor soldering quality. This could lead to increased failures in final product testing or even in the customer's hands. A lack of real-time data prevents Quality Managers from responding promptly to issues as they arise. This delay in response can exacerbate small issues, turning them into significant bottlenecks. If a critical machine starts producing off-spec components and the issue is not identified and resolved quickly, it could cause a backlog in production, impacting delivery timelines and increasing costs due to wasted materials and time. Advanced risk assessment tools must predict potential failures before they occur by using historical data and predictive analytics to forecast likely problems based on patterns and trends, allowing preventative measures to be put in place.
Scalability Issues
Struggling with complex jobs and failing to meet changing requirements.
Flexibility and functionality are mandatory to handle advanced quality checks, adapt to unique customer specifications, and respond to changing industry standards or customer demands on the production floor. The limitations of a QMS often arise from its foundational design, which is typically generic and not customized to meet the specific needs of modern production floor environments. This generic approach fails to address the complexities that contemporary production settings demand.
In industries like automotive or aerospace manufacturing, where precision and adherence to exacting standards are crucial, a simplified system may not support the intricate quality checks required for parts that must meet rigorous safety and performance criteria. Such software might not integrate with advanced diagnostic tools or capture the detailed data needed for complex analyses, like stress tests or compliance checks against evolving safety regulations. Plus, individual customers may have specific demands regarding product specifications, packaging, or batch testing, which can vary significantly from one order to another. Not having the capability to adjust workflows or documentation processes to cater to unique specifications may lead to errors in fulfilling customer orders and, consequently, customer dissatisfaction and potential loss of business.
As new technologies emerge and markets evolve, manufacturers must adapt their processes quickly to remain competitive and compliant. QMS software must be able to accommodate new standards or incorporate the latest best practices. This rigidity can result in a manufacturing operation that lags behind industry advancements, fails to meet new regulatory requirements, or cannot leverage new technologies to improve product quality and operational efficiency.
Certification and Audit Risks
Incomplete and Inconsistent Documentation
Incomplete or inconsistent documentation can have significant repercussions on the production of quality finished products and the ability of a company to pass regulatory audits. When documentation is superficial, key details about processes, quality controls, and compliance measures may be omitted or inaccurately reported. This lack of precision can lead to inconsistencies in product manufacturing, as operators might not have clear or complete instructions on executing tasks according to industry standards. For example, if QMS software fails to provide comprehensive details on equipment calibration, operators might use improperly calibrated machines, resulting in products that deviate from quality specifications.
Moreover, incomplete documentation hampers a company's ability to demonstrate compliance with regulatory standards during audits. Auditors rely heavily on thorough documentation to trace the production process from start to finish, ensuring that all quality control measures are in place and effectively implemented. If the documentation does not accurately reflect the processes or fails to include all necessary records, it raises red flags for auditors, potentially leading to failed audits. This can result in legal and financial consequences, such as fines, recalls, or loss of certification, which can severely affect the company's reputation and marketability.
In comparison, a comprehensive document management system will also solve the accountability and document security conundrum, which is: “Who had access to these
critical files? Who changed our Operating Procedures? Who signed off on them?”
And finally, well-configured software can streamline and expedite audits, reduce the stress of audit preparation, and save countless hours annually.
Stay tuned for Part Three, where we will continue discussing the crucial downsides of simplified QMS software and how it can lead to inadequate outcomes.
Author: Ron Belts, Director Of Strategic Accounts for Bluesteak | Bright AM™
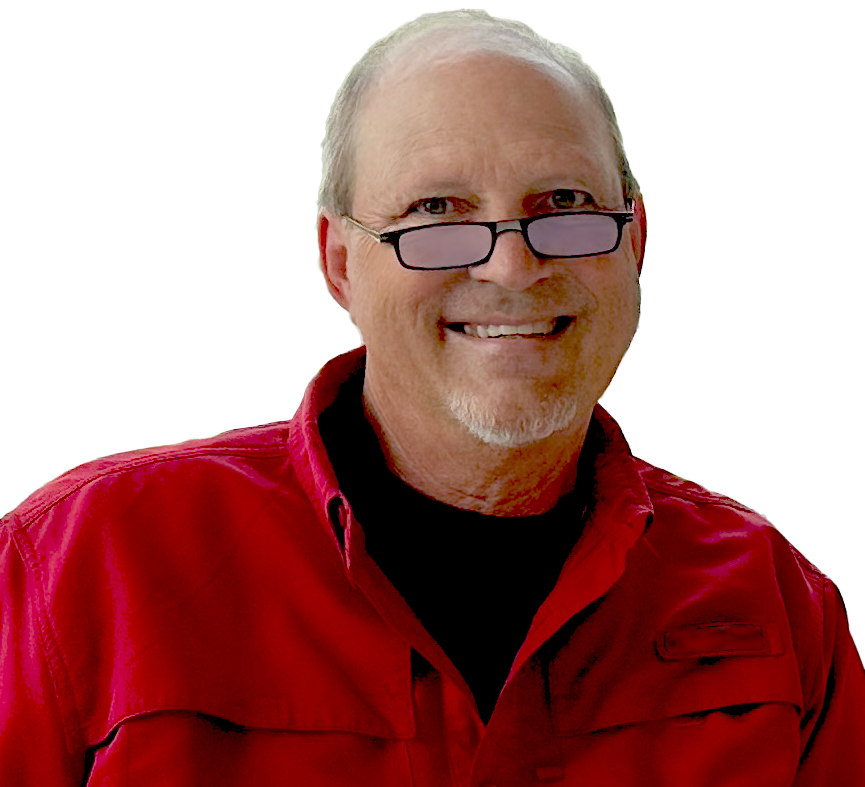
About Bluestreak™:
Bluestreak™ is a fully integrated Quality Management System (QMS), a powerful Manufacturing Execution System (MES) designed for the manufacturing environment and service-based manufacturing companies ( metal-treating/powder-coating, plating, heat-treating, forging, and metal-finishing), businesses that receive customers’ parts, perform a process (service) on them, and send those parts back to the customer). Companies need MES software tailored to specific functionality and workflow needs, such as industry-specific specifications management, intuitive scheduling control for staff and machinery maintenance, and the ability to manage work orders and track real-time data. If different work centers on the production floor aren’t “speaking” to each other via the MES, the data loses value and becomes disjointed or lost in disparate silos.
Bluestreak | Bright AM™ is an MES + QMS software solution specifically designed to manage and optimize the unique requirements of Additive Manufacturing’s production of parts and powder inventory usage.
Comments