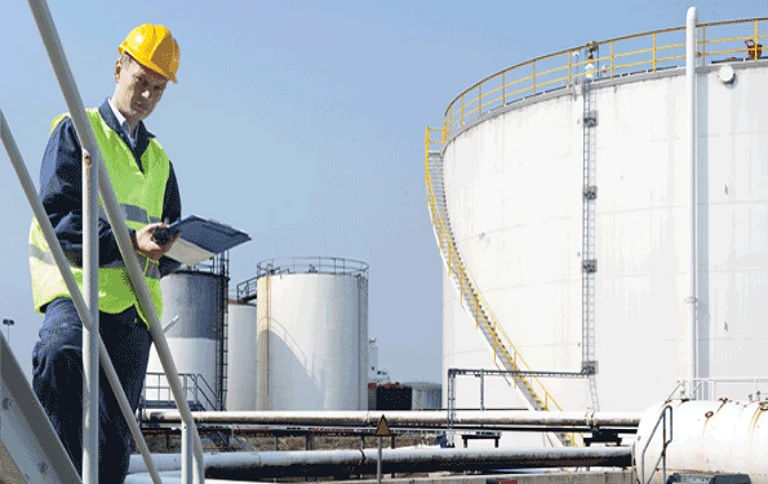
Bluestreak Reading Time: 3 minutes
Quality Audit Reports
If your audit is approaching and you’re already concerned about lengthy downtimes and tying up your departments, it’s time to set up a new reporting system to facilitate your audit process. Quality audits aren’t just something to pass. They help ascertain customer relationships, build streamlined processes, and offer new perspectives on company decisions of all kinds.
Your quality audit reports are directly responsible for your audit outcomes, and handling those reports is a top priority. When you have your reports in order, you can streamline your audit process to ensure that it doesn’t take up too much time, while still getting the insights that you need to move forward.
Unify data to a single source of truth
You already know that data spreads across multiple departments, and each department has its own system. You also know that:
Gathering data is difficult because data is full of missing pieces and mistakes.
No one can see past histories, so it’s difficult to remember what’s happened in past audits.
Audits throw curveballs, and systems can’t create usable reports on the fly, sending everyone scrambling.
Getting data under control is the single most significant step to producing quality audit reports. With a unified source of truth, you can gather the data you need while preparing for audit time, and you’ll have the chance to pull reports requested at the last minute.
You can do this by creating an automated reporting system that removes human error from data entry and eliminates the department-by-department methodology in favor of one consistent entry method. You won’t have duplicate or missing data, and each department’s reporting will be accurate.
You’ll also have a digital “paper trail,” one that tracks past audits, handles the progression of specifications, and provides a quote-to-invoice workflow with notations for special orders or alterations to the usual production. With everything in the same place, you’ll have a unified dashboard to build your reports—no more hunting down department heads or wondering if the information is accurate or complete.
Dig into the potential of automation
Your audit could be going slowly because you have too many manual processes. A work order comes in and someone notates it. Specifications change and communication is hands-on. Everyone works with a different system. Removing as many manual processes as possible through automation gives you time back.
Reporting is also fraught with human error. When different departments work with their own systems, you end up with information gaps and missing information. It’s challenging to establish a chain of responsibility, and following up with past audits can fall through the cracks. When you automate elements of your process, you can improve the data coming into your system. This automation:
Includes documentation of work orders, specifications, and processes
Removes human error due to incorrect or missing data entry
Allows all stakeholders to access required data and tags changes or comments
Establishes a trail of responsibility, accountability, and updates
You’ll have a robust reporting and communication system that can provide the right data for the questions that your auditor asks. You’ll have removed as much human error as possible, as well as the burden that departments have to report everything through a manual process.
Consider what auditors need
As you work through audits, performance indicators and metrics that auditors need should be added to a convenient dashboard. If your dashboard doesn’t have the metrics that your quality auditors are already looking for, it’s more difficult to build a report and track changes that occur because of audit results. You need to align your dashboard to auditor requirements because:
These indicators can drive improvements.
You’ll have customized dashboard metrics for new insights.
Dashboards serve a dual purpose: the smoothing of audit cycles and data-driven decision-making.
For all this, you’ll need a comprehensive, connected, and integrated dashboard. It’s not just the metrics that you want to see; it’s the metrics that your quality auditors look for each time they complete an audit. While these metrics naturally overlap, getting your dashboard as aligned as possible with auditors’ requirements helps put audits front and center.
With each subsequent audit, you’ll have the metrics that your auditor wants to see, as well as the alignment from previous audits. This means audits will get faster.
Conclusion
Creating better quality audit reports helps cut down on the time spent searching for information, flagging and correcting errors, and creating reports that don’t answer the right questions. All audit information will be right in your dashboard, and you’ll be able to make data-driven decisions.
Bluestreak’s dashboard capabilities put all information into a single source of truth, available for all stakeholders and customizable to create reports in seconds. Your dashboard will become one of the most useful tools that you have for passing audits and using the results to create long-term success and growth for your organization. It’s time to find out how Bluestreak’s unique systems can cut your quality audit time in half.
If you’re tired of business being halted for lengthy audit processes and want to see how automation not only cuts your audit times in half but also helps build better relationships with your customers, contact us for a free demo today!
About Bluestreak™:
Bluestreak™ is a powerful Manufacturing Execution System (MES) and a fully integrated Quality Management System (QMS), designed for the manufacturing environment and service-based manufacturing companies ( metal-treating/powder-coating, plating, heat-treating, forging, and metal-finishing), businesses that receive customers’ parts, perform a process (service) on them, and send those parts back to the customer). Companies need MES software tailored to specific functionality and workflow needs such as industry-specific specifications management, intuitive scheduling control for both staff and machinery maintenance, and the ability to manage work orders and track real-time data. If different work centers on the production floor aren’t “speaking” to each other via the MES, the data loses value and becomes disjointed or lost in disparate silos.
Bluestreak | Bright AM™ is an MES + QMS software solution specifically designed to manage and optimize the unique requirements of Additive Manufacturing’s production of parts and powder inventory usage.
Comments