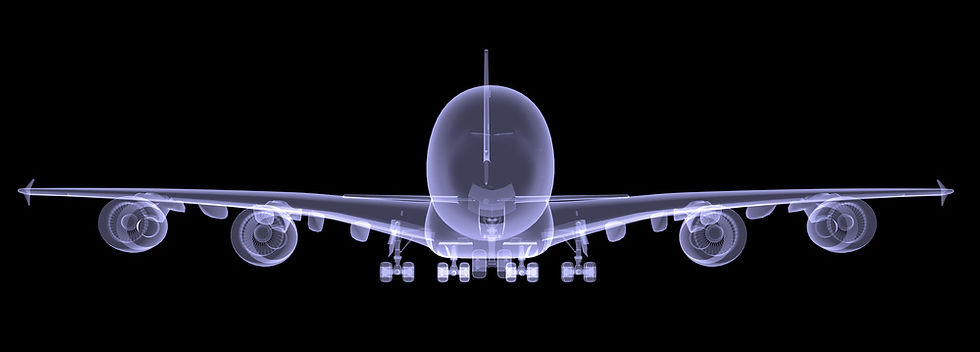
Bluestreak | Bright AM™ Reading Time: 3 minutes
Metal Additive Manufacturing in Aerospace: The Evolution from Initial Triumphs to Industry Revolution
Metal Additive Manufacturing (AM), often referred to as 3D printing, has witnessed significant evolution since its inception. Among the myriad of industries that have benefited from its innovative processes, the aerospace sector stands out from its initial successes to its current transformative impact.
Early Successes: A Glimpse into the Future Metal AM's foray into the aerospace industry began modestly. However, even these initial applications showcased the immense potential of this technology. From lightweight components to intricate designs previously deemed impossible, the early successes provided a glimpse into the possibilities that lay ahead.
Cost Efficiency: Traditional manufacturing methods often require multiple stages and tooling. Metal AM simplified the process, reducing costs significantly.
Design Freedom: Engineers and designers reveled in the newfound liberty to craft intricate designs, thanks to Metal AM. This was especially beneficial in creating complex aerospace components.
Weight Reduction: Given that weight is a critical factor in aerospace, the ability of Metal AM to produce lightweight yet robust parts was a game-changer.
Rising Popularity and Integration: As successes mounted, so did the industry's interest. Major aerospace companies started to recognize the potential benefits and began integrating Metal AM into their production lines.
Customization: Aircrafts tailored to specific needs became feasible. From specialized drones to bespoke commercial jet parts, customization was no longer a distant dream.
Supply Chain Revolution: Metal AM enabled on-demand production, drastically reducing inventory needs and leading to a more responsive supply chain.
Sustainability: With less waste and a reduced carbon footprint, Metal AM emerged as a more sustainable manufacturing option.
Transformation of the Aerospace Industry: Today, Metal AM isn't just an alternative; it's a primary manufacturing method for numerous aerospace applications. The industry has witnessed:
Increased Adoption: From giants like Boeing and Airbus to newer entrants, there's widespread adoption of Metal AM.
Research and Advancements: Constant research has led to even more advanced Metal AM techniques, furthering the tech's applicability and efficiency.
Regulatory Embrace: Recognizing the importance and safety of Metal AM, regulatory bodies have developed standards and guidelines, endorsing its use in critical aerospace parts.
A New Dawn in Aerospace: The Rise of Additive Manufacturing
Globally, a fresh cohort of aerospace engineers are pioneering designs and crafting the future of aero engines and systems, all rooted in the groundbreaking potential of Additive Manufacturing. What was once a mere vision two decades ago is now a tangible reality. Additive Manufacturing has innovated everything from fuel nozzles, Stage 5 and 6 low-pressure turbine blades, to housings and structural components.
Twenty years ago, envision the handful of firms capable of fabricating aerospace components via Additive Manufacturing. Contrast that with today's scenario, where providers span the globe and entire initiatives place Additive Manufacturing at the innovation forefront, even rejuvenating older aircraft fleets. The ability to reproduce parts that are no longer in production, enhance older designs, and reduce maintenance costs makes AM a critical tool in the maintenance, repair, and overhaul (MRO) segment. While the GE LEAP fuel nozzle is often cited for its innovative design in newer engines, GE has explored using similar AM technologies to retrofit and upgrade components in older engines. For example, older aircraft designs might not have the advanced cooling systems present in newer models. Through metal AM, tailored cooling components that fit perfectly within the existing structure of vintage planes can be produced, improving efficiency and safety.
Across the aviation landscape, the game is changing. From engine parts to critical structural components in aircraft and satellite tech, Additive Manufacturing is proving its mettle. Over the recent 3-5 years, a pronounced uptick has been observed in instances where AM-designed parts have replaced those created through traditional means and this accelerated embrace of AM technologies has ushered in a myriad of benefits: 1. Reduced Costs 2. Quicker Lead Time
3. Flexible Design and Methodologies
Moreover, with metal AM's adoption, the aviation world looks forward to diminished CO2 emissions in both manufacturing and end use due to decreased fuel consumption – a promising stride towards enhanced sustainability.
This revolution hasn't materialized out of the blue. Persistent and methodical adoption of 'radical' metal AM techniques, namely Powder Bed Fusion (PBF), Directed Energy Deposition (DED), and Binder Jetting (BJT), have set the stage for unparalleled innovation, from part design to alloy invention. As major OEMs and top-tier suppliers tentatively set the ball rolling, this narrative dives deep into the breakthroughs achieved, spotlighting pivotal instances like turbine blades in engines and intricate communication tools in satellites. The guarded nature of the aerospace sector, with its profound hesitations and robust defenses surrounding new AM applications, remains a perplexing aspect to insiders and those within the AM value chain alike.
Technologies, supported by an ever-expanding roster of machinery suppliers globally, have genuinely revolutionized the way the aerospace sector operates. It has facilitated the creation of intricate designs and featherweight structures while amplifying component efficiency, all while trimming down production costs. A noteworthy achievement of these methods is the capacity to circumvent intricate assembly and fusion procedures by integrating numerous components into one unified part design. This seamless integration not only streamlines the manufacturing process but also paves the way for innovations in design and functionality.
When you’re in the business of large-scale Additive Manufacturing, you need a Quality Manufacturing System built for the task. Once you have the right software solution in place, Additive Manufacturing can become an efficient and cost-effective way of doing business.
Bluestreak | Bright AM™ is the leading provider of compliance and quality management software, trusted by the world’s strongest brands.
Why not take a minute to find out more about our Quality Management and Manufacturing Execution System built in one platform? Contact us for a demonstration!
Bluestreak | Bright AM™ is an MES + QMS software solution specifically designed to manage and optimize the unique requirements of Additive Manufacturing’s production of parts and powder inventory usage. About Bluestreak™:
Bluestreak™ is a powerful Manufacturing Execution System (MES) and a fully integrated Quality Management System (QMS), designed for the manufacturing environment and service-based manufacturing companies ( metal-treating/powder-coating, plating, heat-treating, forging, and metal-finishing), businesses that receive customers’ parts, perform a process (service) on them, and send those parts back to the customer). Companies need MES software tailored to specific functionality and workflow needs such as industry-specific specifications management, intuitive scheduling control for staff and machinery maintenance, and the ability to manage work orders and track real-time data. If different work centers on the production floor aren’t “speaking” to each other via the MES, the data loses value and becomes disjointed or lost in disparate silos.
Comments