How to Reduce Scrap in Manufacturing
- Jean Wenzel
- Feb 2, 2022
- 4 min read
Updated: Aug 14, 2023
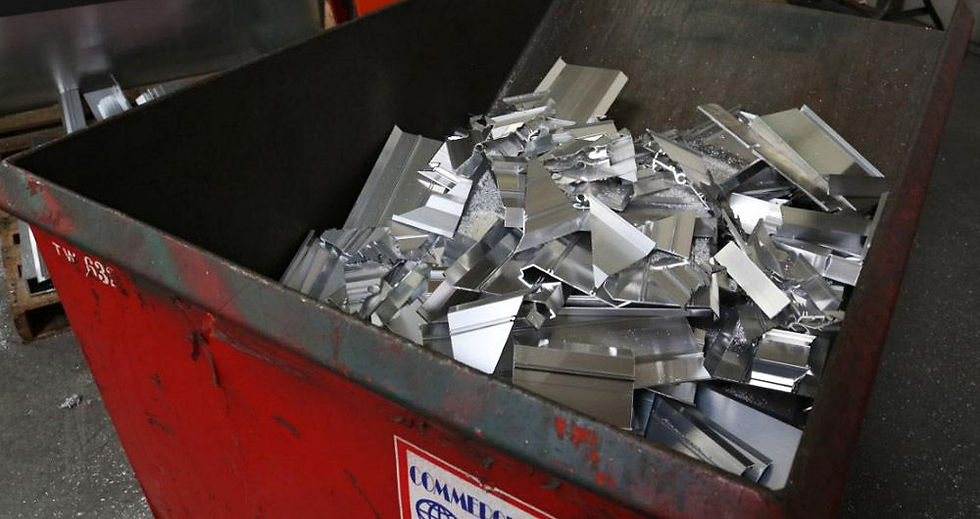
Bluestreak Reading Time: 3 minutes
What difference would it make in your shop if you could reduce scrap by 25% or more?
In manufacturing, some scrap is a natural consequence. However, that doesn’t mean you need to accept it—or at least, not all of it. There are ways to reduce the amount of scrap that you produce by using the right methods and technology.
The concept is simple: lower scrap means higher profit margins.
Scrap Measurement
When evaluating how to reduce scrap in manufacturing, the first step is to measure your level of scrap. It’s amazing how many manufacturers do this incorrectly or don’t do it at all. For example, some manufacturers measure scrap against sales revenues instead of production costs. But this doesn’t adequately represent the cost of scrap, as it will vary depending on monthly sales.
Here’s the formula that you should use when measuring how to reduce scrap in manufacturing: Gross Scrap / Cost of Good Produced.
On a project basis, manage your expected (budgeted) amount of scrap versus the actual amount of scrap. If there’s a discrepancy, that’s one of the first places to look. Then, measure improvement against your baseline when implementing control processes. Even if you deem the amount of scrap to be acceptable, that doesn’t mean it’s not worth investigating other process efficiencies. Any scrap, waste, or rework that you can eliminate leads to higher profits.
How to Reduce Scrap in Manufacturing
You can reduce scrap in manufacturing by implementing these five steps:
Having qualified equipment and operators
Eliminating information silos
Having proactive management
Having a scrap materials plan
Having quality management software (QMS)
Having Qualified Equipment and Operators
When equipment and operators are properly qualified, scrap goes down. This means ensuring that equipment is calibrated correctly and that maintenance has been done. Poor maintenance habits and improper calibration will create additional scrap and potentially unsafe conditions.
Make sure your operators are also qualified for the task at hand. If not, the work may be sub-par. Your operators should be trained on the process and the equipment.
If they’re not scheduled at the same time that the equipment is available, it may slow your production schedule.
Eliminating Information Silos
Without real-time information available to everyone who needs it, scrap is inevitable. If you’re using a manual process or the wrong software, your operators may encounter these conditions that lead to increased scrap:
Outdated information is used.
Updated information doesn’t get passed on to operators.
Change orders and process changes are not documented.
Papers get lost or misplaced.
The right real-time QMS solution can solve these problems.
Having Proactive Management
If you have acceptable raw materials and stable machining, nearly every other problem tracks back to either human error and/or process problems. When there’s a large amount of scrap or you’re unhappy with the level of scrap, it means you need more proactive management. This should include:
Total quality management (TQM)
Corrective and preventative actions (CAPA) program
Qualifying programs
If you’re waiting until you catch nonconformance's to address quality, you have inefficient systems. A focus on TQM is a strategic and systematic approach to quality through processes. When this proactive quality management thinking is embedded in your culture along with CAPA and qualifying programs, quality improves and scrap reduces.
Having a Scrap Materials Plan
Some amount of scrap is simply unavoidable. Besides the cost of labor and rework, you’re also looking at materials costs. Instituting a formal scrap materials plan should examine:
Can products or components be refurbished or repurposed?
Can scrap be recycled?
How can you avoid dumping fees?
Your first thought for scrap should be repurposing. Re-using scrap metal, for example, is less resource-intensive than using virgin materials. Plastic can often be repurposed for component parts. Every piece of scrap that you can repurpose can save you money, versus having to pay for it be hauled away or dumping fees. If scrap can’t be repurposed, then make sure you’re recycling it to recover whatever costs you can.
Bluestreak manufacturing execution system (MES) and quality management system is a single-platform software solution that manages the entire production pathway with real-time shop floor tracking. Features include:
Eliminating information silos
Measuring and monitoring processes
Having continuous process improvement
Real-time tracking on every step
Bluestreak QMS + MES can help qualify equipment and operators, track maintenance and testing, and facilitate proactive scrap management.
Want to Learn How to Reduce Scrap in Manufacturing? Try Bluestreak QMS + MES
Learn how to reduce your rework and scrap by at least 25%.
Bluestreak’s MES + QMS solution helps service-based manufacturers drive quality straight down to the production floor to minimize scrap and rework and therefore, protect their profit margins.
If you’re ready to leave manual, time-consuming service-based manufacturing tasks in the past, drastically reduce your scrap and rework percentage, gain visibility of your production floor processes, and build better relationships with your customers, contact us for a free consultation today!
About Bluestreak™:
Bluestreak™ is a powerful Manufacturing Execution System (MES) and a fully integrated Quality Management System (QMS), designed for the manufacturing environment and service-based manufacturing companies ( metal-treating/powder-coating, plating, heat-treating, forging, and metal-finishing), businesses that receive customers’ parts, perform a process (service) on them, and send those parts back to the customer). Companies need MES software tailored to specific functionality and workflow needs such as industry-specific specifications management, intuitive scheduling control for both staff and machinery maintenance, and the ability to manage work orders and track real-time data. If different work centers on the production floor aren’t “speaking” to each other via the MES, the data loses value and becomes disjointed or lost in disparate silos.
Bluestreak | Bright AM™ is an MES + QMS software solution specifically designed to manage and optimize the unique requirements of Additive Manufacturing’s production of parts and powder inventory usage.
Comments