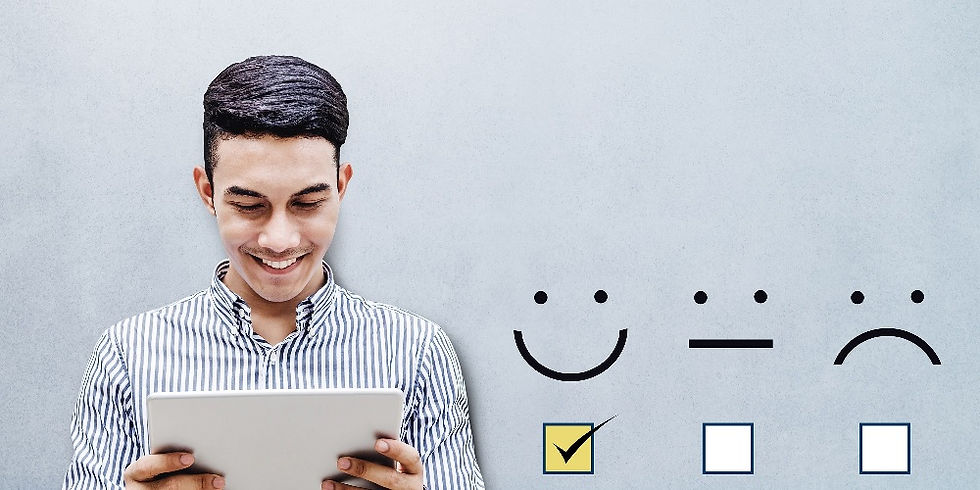
Bluestreak Reading Time: 3 minutes
When it comes to manufacturing, two of the most important things to ensure happy customers and produce solid profit margins are consistency and reliability.
The Benefits of Consistency and Reliability for happy clients
Creating consistency and reliability is the byproduct of a stringent quality control program that creates manufacturing compliance. As a result, manufacturers will benefit from:
Optimal use of resources (less waste, scrap, and rework)
Lower cost of production
More efficient energy usage
Lower labor costs
Happy clients
With the increased pressure to provide quality work with fewer people and less capital, it’s become even more challenging. However, failing to reliably produce consistent quality is a recipe for poor manufacturing compliance, decreasing customer satisfaction, and fewer renewal orders.
It takes a cultural shift to embrace a quality mindset—and the use of manufacturing execution and quality management software (MES + QMS).
The Struggle with Manual Compliance
One of the things that hold manufacturers back from adopting this quality mindset is a lack of the right tools to manage the entire production pathway. Most manufacturers still depend on manual methods and paper forms to gather info and manage audits and inspections on the shop floor.
An inspection report is an essential part of manufacturing compliance. Yet, the daily data collection, completion of reports, and sharing across the organization are time-consuming and inefficient. So much can go wrong in the time between when a form is filled out, shared with office staff, re-entered manually into databases, and then stored away in a filing cabinet. Lost or damaged forms, human errors, and alterations can compromise the process.
Without the visibility to collect and view data in real time in an organized manner, it can become difficult to spot inefficiencies or catch problems that can be corrected. Critical information can be hard to find, and manufacturing compliance becomes that much more difficult.
When trying to meet industry specifications and guidelines, such as those required by MedAccred for the medical device supply chain, manual processes lack the visibility required to meet regulatory requirements.
With a real-time management system, the digitization of the data at every step of the way ensures that everybody has the information that they need during manufacturing. Also, the data is readily available when it’s time for an audit. This can save days’ worth of work. Fortunately, real-time paperless workflow and automation software are no longer reserved for just the largest manufacturers with big budgets. They’re affordable for any manufacturer, and they improve compliance, reduce audit times, and improve quality.
How the Right MES + QMS Can Solve Manufacturing Compliance
Bluestreak MES + QMS uses advanced quality tracking and provides manufacturers with the ability to control quality characteristic requirements per specification standards. The Advanced Specifications Manager can handle management support for industry specifications, including:
AIAG
API
AMS
AS
ASME
ASTM
ISO
NADCA
NADCAP
SAE
TS
Any internal and Prime specifications
Bluestreak’s innovative solution enables businesses to conform to specification requirements every time, while automatically creating and maintaining a fully documented audit trail containing management specification documents, requirements, media, and more importantly, automatically cross-referenced specifications to everything that they impact—processing, equipment, personnel, vendors, etc.
Bluestreak MES + QMS reduces human error in quality data entry and reporting with enforceable risk analysis built into your QMS. For example, trying to implement the rounding and converted units manually by training inspectors is difficult to do and prone to numerous reporting errors. The only realistic option is to have it done automatically by your QMS.
Managing the Production Pathway
Managing manufacturing compliances demands transparency in the production pathway. Bluestreak MES + QMS allows manufacturers to monitor all work in progress, at every stage of processing, from contract review to shipment. Via the “Captive Departments” feature, Bluestreak can track all job routing for every part or just certain parts within specific departments. It can capture any kind of production data during tracking, as well as qualify personnel, equipment, and outside vendors in real time.
It also empowers operators by giving them access to critical information such as processing data, part pictures, drawings, and purchase orders. Everything they need and every piece of data will always be up to date and accurate.
Improved Manufacturing Compliance = Happy Customers, More Profitability
When it comes to manufacturing compliance, Bluestreak MES + QMS ties quality control and quality assurance directly to individual work centers and processing steps on the production floor. By eliminating silos of disjointed data, systems are more efficient. This leads to less scrap, waste, and rework. It creates more productive workflows and greater manufacturing compliance. It also improves consistency and reliability. That means happy customers and improved profit margins.
Bluestreak’s MES + QMS solution helps service-based manufacturers drive quality straight down to the production floor to minimize scrap and rework and therefore, protect their profit margins. If you’re ready to leave manual, time-consuming service-based manufacturing tasks in the past, drastically reduce your scrap and rework percentage, gain visibility of your production floor processes, and build better relationships with your customers, contact us for a free consultation today!
Comments