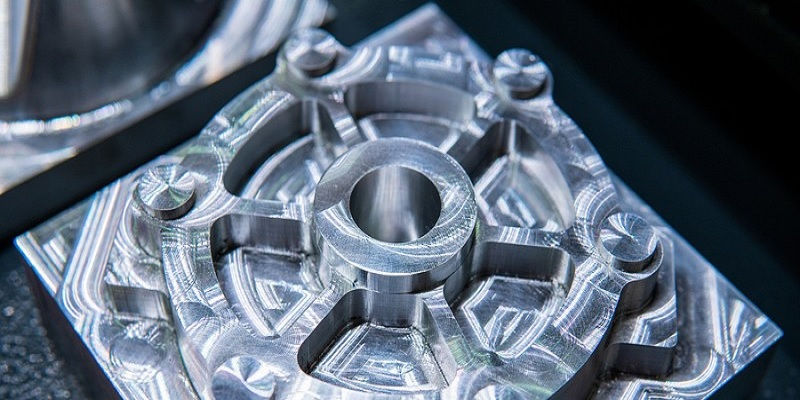
Bright AM Reading Time: 3 minutes
Lean methodology is an approach to reduce waste and improve productivity.
It’s designed to get rid of anything that doesn’t add value to the production chain, which can be as simple as moving raw materials closer to the production floor or as complex as reengineering the entire workflow.
Five core principles form the basis of deploying the Lean manufacturing philosophy:
Identify value: Value is defined by customers. By understanding what customers value, manufacturers can adapt to eliminate waste and reduce costs. This allows manufacturers to produce parts at the optimal price and improve profitability.
Map the value stream: Record and analyze the flow of materials and information needed to produce parts to identify waste. This should include everything from order and production to shipping.
Create flow: Identify and eliminate functional barriers and interruptions to anything that impacts workflow.
Establish a pull system: New work begins only where there is demand. This creates reduced inventory levels and less overhead.
Pursue perfection: Known as Kaizen, this process provides continuous optimization and continued elimination of waste.
The Benefits of Lean Manufacturing
By analyzing the entire workflow with a critical eye, manufacturers can sometimes gain unique insights. Let’s look at the example of MicroMetl, a heating and air conditioning equipment manufacturer. They tracked the production pathway of a single part being manufactured. From start to finish, that part traveled more than a mile and a half inside the plant. By redesigning their workflow, they were able to cut down travel time to just 100 feet. Along with other Lean approaches, they trimmed production times significantly and reduced indirect labor costs by 21%.
While travel time isn’t as significant an issue for most Additive Manufacturers, taking an in-depth look at each phase of the operation can yield similar results. For example, how much time is lost using manual processes across the entire build? This can also lead to lost or misplaced data, inaccurate or incomplete work orders, or failing to record the data necessary to move to the next phase. Deploying Additive Manufacturing (AM) software that allows for real-time data that’s visible to everyone in the production pathway and tied to work orders can eliminate a significant challenge.
Benefits of Lean manufacturing include:
Less waste, scrap, and rework
Fewer defects
Fewer machine breakdowns
Lower inventory levels
High levels of stock turnover
Increased output per work-hour
Changes accommodated more easily
More efficient operations
Companies that embrace Lean manufacturing principles expand their capacity, shorten their production times, and improve their margins. It’s hard to argue with that!
AM Supports Lean Manufacturing Principles
One way that custom manufacturers can embrace Lean methodology is by expanding their use of Additive Manufacturing itself. After all, AM creates efficiencies that traditional manufacturing process can’t, including:
Faster and easier prototyping
Easier customization
Less reconfiguration of machines
Greater freedom during the design phase
Improved consistency
Reduced lead times
The reduction in the time that it takes to move goods from design to completion can reduce the overall cost of production.
Achieve Scalable Growth with Lean Manufacturing Principles
Deploying Lean manufacturing strategies takes two commitments on the part of Additive Manufacturers: people and technology.
Lean manufacturing takes a holistic approach to the workplace. Since it includes every phase of operations and every step of production, it requires buy-in from everyone involved. One of the roadblocks for Lean manufacturing is the fear of change. Employees worry that a more efficient process might cost them their job. Even when they know that there is a better way to do things, teams can often be resistant to change.
Additive Manufacturing demands the right technology to manage the production pathway from order to delivery. That’s where Bluestreak | Bright AM comes in. Bluestreak | Bright AM is an extensible, real-time MES/QMS designed exclusively for the Additive Manufacturing industry.
Other MES, QMS, ERP, and MRP systems lack the built-in functionality that Additive Manufacturing requires. Currently being used by some of the world’s largest AM production facilities, Bluestreak | Bright AM has the tools you need to create Lean manufacturing strategies for Additive Manufacturers of any size.
Bluestreak allows for rapid changes and ensures that everyone has the information they need. It enables real-time data flow, tracking, and qualifications of equipment and personnel, while tracking all job routing for all parts. It eliminates information silos and provides powerful quality control tools to drive quality management and stellar efficiency through the entire AM process.
Contact Bluestreak | Bright AM for a Demo
If you would like to learn more about how Lean manufacturing can help in custom manufacturing, get in touch with the Additive Manufacturing experts at Bluestreak | Bright AM for a demo. Let us show you how using Bluestreak | Bright AM with a Lean manufacturing process can help you scale your custom manufacturing business.
When your quality control process needs improvement, you’re wasting time and money. You are also putting future business at risk, and we know how small of an industry this can be. Dissatisfied customers tend to spread the word to their colleagues, which can hurt future sales. Recognize the warning signs and take action today by contacting Bluestreak | Bright AM.
Comentarios