
Bluestreak™ Reading Time: 5 minutes
Heat-Treating Aerospace: Enhancing Performance and Reliability
Heat treatment is a critical process in the aerospace industry, where components are subjected to extreme conditions and rigorous demands. These treatments are vital for enhancing the mechanical properties, durability, and overall performance of materials used in aircraft and spacecraft. The aerospace sector employs various heat-treating techniques, each tailored to meet specific requirements and challenges. In this article, we'll delve into some of the most popular treatments utilized in aerospace and explore their significance and applications.
Heat-treating Aerospace for Performance and Reliability involves heating and cooling materials, typically metals and alloys, in a controlled manner to alter their microstructure and properties. The primary objectives of heat treatment in aerospace are to enhance strength, hardness, toughness, and resistance to corrosion and fatigue.
Solution Heat Treatment
Solution heat treatment is a common method employed in the aerospace industry, particularly for aluminum alloys. It involves heating the material to a specific temperature, known as the solutionizing temperature, followed by rapid cooling to retain a homogeneous solid solution of alloying elements. This process eliminates internal stresses and enhances the material's ductility and machinability.
Significance in Aerospace
Aluminum alloys are extensively used in aerospace due to their lightweight properties and high strength-to-weight ratio. Solution heat treatment is crucial for these alloys as it improves their formability and allows for intricate shaping processes during aircraft manufacturing. Additionally, solution-treated alloys exhibit enhanced resistance to fatigue, making them suitable for critical aerospace components subjected to cyclic loading.
Aging
Aging is a post-solution treatment used to further enhance the mechanical properties of alloys, particularly aluminum and titanium alloys. The process involves heating the material to a lower temperature than the solutionizing temperature, followed by controlled cooling. This allows for the precipitation of fine particles within the alloy matrix, which strengthens the material through a process known as precipitation hardening or age hardening.
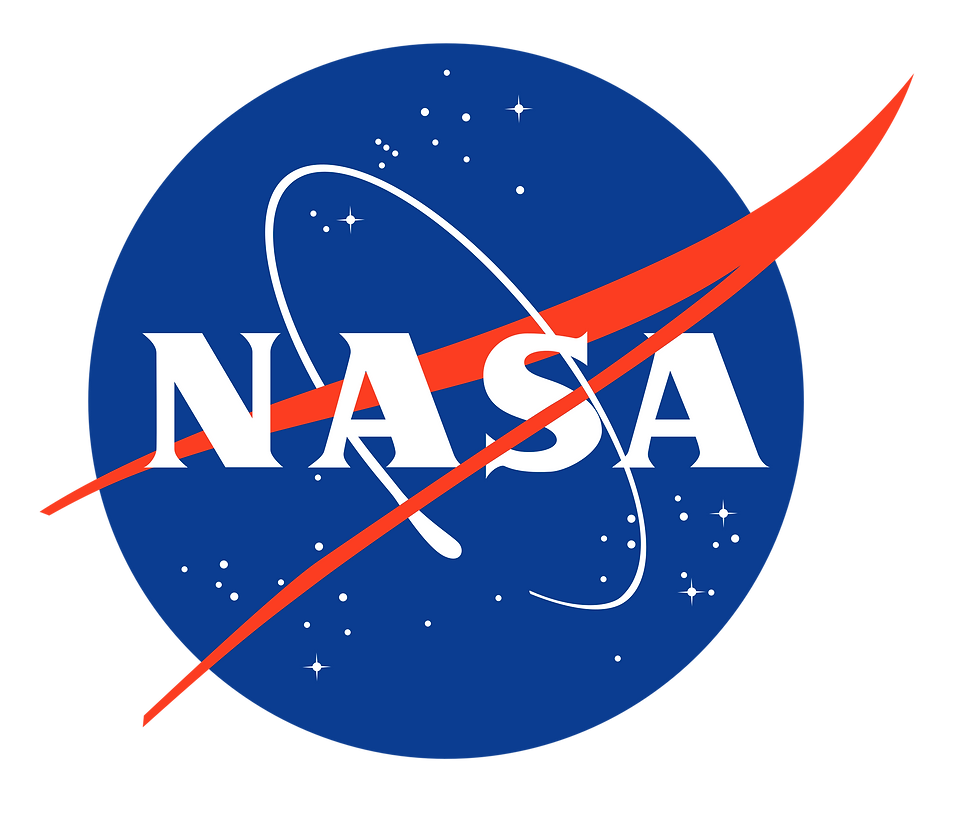
NASA conducts various research studies and publishes findings related to aerospace materials, including the effects of aging treatments on mechanical properties. To find relevant studies or reports, you can visit the NASA Technical Reports Server (NTRS) and search using keywords such as "aging treatments aerospace components" or "mechanical properties aerospace materials" which will help you find relevant research papers or reports published by NASA or affiliated researchers.
Significance in Aerospace
Components such as aircraft structural elements, landing gear, and engine parts benefit significantly from aging treatments, as they require superior mechanical properties to withstand extreme operating conditions.
Carburizing
Carburizing is a surface hardening treatment primarily applied to low-carbon steels and certain alloy steels. The process involves introducing carbon into the surface layer of the material at elevated temperatures in a carbon-rich atmosphere. This forms a hardened case with high carbon content, while the core retains its original properties.
Significance in Aerospace
While not as prevalent as in other industries, carburizing finds applications in aerospace for components requiring wear resistance and improved fatigue strength, such as gears, shafts, and bearings. However, due to the susceptibility of carburized components to hydrogen embrittlement, extensive testing and quality control measures are necessary to ensure their reliability in aerospace systems.
Testing Requirements
Hydrogen Embrittlement Testing Carburized components undergo specialized testing procedures to assess their susceptibility to hydrogen embrittlement. This involves subjecting samples to controlled environments where hydrogen ingress can occur, simulating the conditions encountered during service. Various test methods, such as the slow strain rate test (SSRT) and the hydrogen embrittlement test, are employed to evaluate the material's susceptibility to embrittlement and quantify its impact on mechanical properties.
Mechanical Testing Comprehensive mechanical testing is conducted to assess the integrity and performance of carburized components under simulated operating conditions. Tensile testing, hardness testing, fatigue testing, and impact testing are among the essential tests performed to verify the material's strength, toughness, and resistance to fatigue failure.
Microstructural Analysis A microscopic examination of the material's microstructure is essential to detect any abnormalities or defects resulting from the carburizing process. Metallographic analysis, including optical microscopy and scanning electron microscopy (SEM), provides insights into the distribution of alloying elements, the presence of carbides, and any signs of hydrogen embrittlement-induced degradation.
Nitriding
Nitriding is a surface hardening process predominantly used for ferrous materials, including steels and cast irons. Unlike carburizing, which introduces carbon, nitriding introduces nitrogen into the material's surface layer to form hard nitride compounds. This results in increased surface hardness, wear resistance, and fatigue strength without significant dimensional changes.
Significance in Aerospace
Nitriding offers several advantages for aerospace applications, particularly in components subjected to high temperatures, corrosive environments, and abrasive wear. Engine components, such as crankshafts, camshafts, and valves, benefit from nitriding due to the improved surface hardness and resistance to galling and fretting under extreme operating conditions.
Vacuum Heat Treatment
Vacuum heat treatment involves subjecting materials to elevated temperatures in a vacuum environment, eliminating the presence of oxygen and other reactive gases. This prevents oxidation and contamination of the material surface, ensuring uniform heating and cooling rates throughout the process.
Significance in Aerospace
In aerospace, where component integrity and purity are critical, vacuum heat treatment is preferred for materials such as titanium alloys, superalloys, and tool steels. Components destined for high-temperature applications, such as turbine blades and structural elements in rocket propulsion systems, undergo vacuum heat treatment to optimize their mechanical properties and ensure long-term reliability in service.
Conclusion
Heat treatment plays a vital role in shaping the performance and reliability of materials used in the aerospace industry. Each heat-treating treatment offers unique advantages tailored to specific application requirements, whether it's enhancing strength, hardness, wear resistance, or thermal stability. From solution heat treatment and aging of aluminum alloys to surface hardening processes like carburizing and nitriding, aerospace manufacturers employ a diverse array of techniques to meet the demanding challenges of modern aircraft and spacecraft design. Through meticulous control and optimization of heat treatment processes, aerospace engineers can ensure the integrity and longevity of critical components operating in the most stressful environments imaginable.
About Bluestreak™:
For over eighteen years, Bluestreak™, a powerful Manufacturing Execution System (MES) and a fully integrated Quality Management System (QMS) has been the software of choice for heat treaters around the world including service-based manufacturing companies (metal-treating/powder-coating, plating, forging, and metal-finishing), businesses that receive customers’ parts, perform a process (service) on them, and send those parts back to the customer). Companies need MES software tailored to specific functionality and workflow needs such as industry-specific specifications management, intuitive scheduling control for staff and machinery maintenance, and the ability to manage work orders and track real-time data. If different work centers on the production floor aren’t “speaking” to each other via the MES, the data loses value and becomes disjointed or lost in disparate silos.
View the Bluestreak Overview Video.
Bluestreak | Bright AM™ is an MES + QMS software solution specifically designed to manage and optimize the unique requirements of Additive Manufacturing’s production of parts and powder inventory usage.
Comments