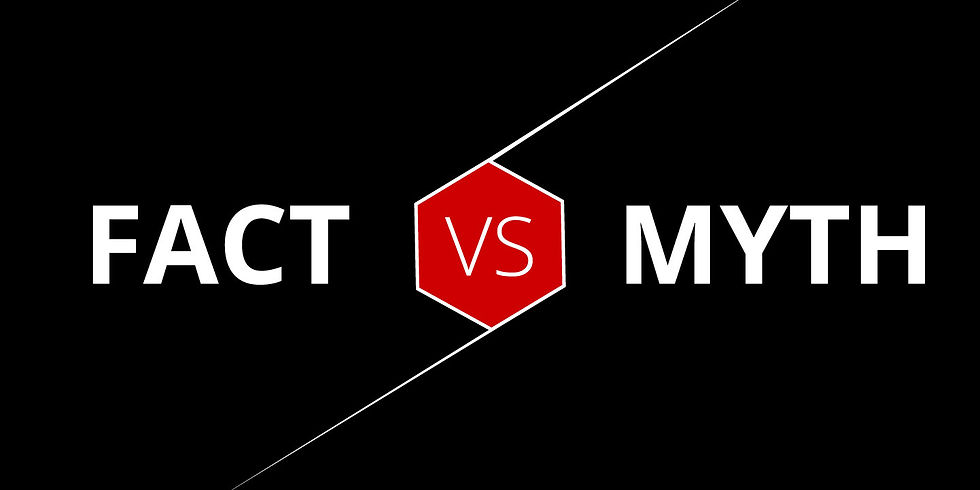
Bluestreak Reading Time: 6 minutes
Despite having been around for over 35 years, 3D printing is often seen as a nascent technology. While it undoubtedly has a promising future with continuous advancements expected in the coming decades, it is important to dispel some common misunderstandings or myths about the industry. Bluestreak | Bright AM™, as a leading player in the field of Additive Manufacturing Software (Quality Management + Manufacturing Execution Software), we frequently encounter these misconceptions. Let's explore four misunderstandings about 3D Printing and provide evidence to debunk them.
Misunderstanding #1: 3D Printing is Replacing Traditional Manufacturing
Although Additive Manufacturing (AM) is considered one of the major future trends in the manufacturing industry, it will not completely replace traditional manufacturing. Processes like injection molding, machining, and casting are cost-effective and rapid methods of mass production. AM, on the other hand, offers distinct benefits but is best used in conjunction with other manufacturing methods, rather than as a complete replacement.
Traditional and Additive Manufacturing Strengths
Traditional manufacturing excels in mass production, offering an economical approach to high-volume, low-cost products. For instance, consumer goods such as disposable cutlery, plastic bottles, and packaging materials are not suitable for industrial 3D printing and while 3D printing has made strides in the field of fashion clothing and textiles, mass production of clothing items like t-shirts, jeans, or socks is better suited for traditional manufacturing methods due to high production volumes, various sizes, and complex fabric requirements.
Additive Manufacturing may be a higher-cost option for large-volume production, but it provides customization, part consolidation, and rapid prototyping, enabling businesses to achieve greater freedom and individualization in production. Customization, a key advantage of 3D printing, allows companies to cater to their consumers in ways traditional manufacturing cannot match. Here are six industry examples where companies can excel in offering personalized consumer products tailored to individual preferences:
Personalized Consumer Products
This includes items like phone cases, jewelry, home decor, and accessories. Customers can have their names, initials, or unique designs incorporated into the product, creating a sense of individuality and exclusivity.
Custom-fit Prosthetics and Orthotics
3D printing allows for the creation of custom-fit prosthetic limbs and orthotic devices to produce precise and customized solutions based on individual measurements and anatomical needs. This enhances comfort, functionality, and quality of life for users.
Dental and Medical Implants
3D printing enables the creation of patient-specific implants that perfectly match the unique anatomy of each individual. This customization improves implant success rates, reduces complications, and provides better patient outcomes.
Architectural Models and Prototypes
In architecture and construction, 3D printing allows for the creation of intricate and accurate architectural models and prototypes. These models can be customized to represent specific design elements and demonstrate structural concepts to aid in client presentations. This level of customization helps architects and designers bring their visions to life and make informed decisions.
Unique Art and Design Objects Artists and designers can leverage 3D printing to create one-of-a-kind, intricate, and geometrically complex art and design objects. The ability to customize the form, texture, and details of these objects opens up new creative possibilities that are challenging to achieve through traditional manufacturing methods. Replacement Parts and Spares 3D printing enables the production of customized replacement parts and spares that are no longer available in the market. This benefits industries like automotive, aerospace, and machinery, where specific components may become obsolete over time. With 3D printing, companies can reproduce these parts on demand, eliminating the need for expensive tooling, inventory management, and replacement parts that can be built in remote or combat situations to maintain operational readiness. Here are two examples of how the US Military has been exporting the use of 3D printing parts: 1. In 2014, the U.S. Marine Corps deployed 3D printing capabilities to Camp Leatherneck in Afghanistan. They used 3D printers to produce various replacement parts, including small plastic components and customized vehicle accessories. This initiative aimed to reduce the reliance on traditional supply chains and provide rapid support to troops in the field. 2. In 2018, the USS Harry S. Truman aircraft carrier became the first deployed U.S. Navy vessel to have an onboard 3D printer, allowing for the production of non-critical replacement parts while at sea. This initiative aimed to enhance operational readiness and reduce logistical burdens. Misunderstanding #2: 3D Printing is Only for Rapid Prototyping While 3D printing is indeed used extensively for rapid prototyping, its benefits extend beyond that. Additional advantages of 3D printing include:
Ability to produce complex geometries: Traditional manufacturing techniques such as milling, turning, or casting struggle to produce complex application geometries. When possible, the cost-per-part makes it economically unviable. AM offers engineers unparalleled design freedom to create applications with intricate geometries, whether they are unique, organic, or AI-derived, without incurring additional production costs.
Ability to mass customize and manufacture on demand: Evolving market demands and consumer expectations are pressuring manufacturers in industries like automotive, consumer goods, and medical to deliver customized products. This necessitates production capabilities tailored for single or small-batch production, with design requirements defined by individual customers. Traditional manufacturing methods struggle to accommodate this level of customization.
Ability to prioritize sustainability and reduce the carbon footprint: Traditional manufacturing processes involve wasteful material cutting or shaping, resulting in a larger carbon footprint. In contrast, AM uses only the required amount of material, leverages material recyclability, and adopts carbon-neutral materials to reduce carbon emissions and minimize environmental impact.
Misunderstanding Conception #3: All CAD Files are 3D Printable Computer-aided design (CAD) files are vital for digital design and drafting. While there are strategies and tools to convert CAD files to stereolithography (STL) files using slicing software, the conversion is not always flawless and may leave certain elements of the application weak due to differences in manufacturing strategies. For example, converting a CAD file for a metal application with overhangs of less than 45 degrees to an STL file does not guarantee a successful print. Applications without built-in support structures for acute overhangs and angles would require additional AM design elements for successful printing. Misunderstanding #4: All 3D Printers are the Same While 3D printing technology is based on a common methodology, it encompasses a wide range of solutions, styles, and sizes. Currently, there are seven main types of 3D printing processes used for both metal and polymer additive manufacturing: 1. Material Extrusion 2. Vat Polymerization 3. Powder Bed Fusion 4. Material Jetting 5. Binder Jetting 6. Directed Energy Deposition 7. Sheet Lamination 3D printers come in various sizes, catering to different needs. For instance, desktop printers like FDM (Filament Deposition Molding) models are accessible to everyday users, while industrial-grade printer systems require professional additive manufacturing education and training. Misunderstanding #5: Additive Manufacturing is Cost-Effective There is a common misconception that additive manufacturing, particularly metal industrial 3D printing, is too expensive for businesses to integrate into their production processes. While it's true that industrial-grade metal 3D systems may not be considered "cheap" from a business standpoint, it's essential to view them within the larger context of production. Investing in Additive Manufacturing can benefit an organization's bottom line in several ways, making it a strategic move rather than an additional expense. Here are some key factors that illustrate the potential cost-saving benefits of AM:
1. Reduced Material Waste Traditional manufacturing methods often involve subtractive processes, where the material is cut away to create the desired shape. This results in significant material waste. In contrast, additive manufacturing builds objects layer by layer, using only the necessary amount of material. This reduction in waste leads to cost savings in material procurement and disposal. 2. Streamlined Supply Chains Additive Manufacturing enables decentralized production by bringing manufacturing capabilities closer to the point of need. This reduces reliance on extensive and complex supply chains, minimizes shipping costs, and shortens lead times. By producing parts on-site or locally, organizations can save on transportation expenses and optimize inventory management. 3. Elimination of Tooling Costs Traditional manufacturing methods often require expensive tooling, such as molds or dies, to produce specific parts. These tools can be time-consuming and costly to create. In contrast, 3D printing eliminates the need for most tooling, as parts can be directly printed from digital designs. This eliminates tooling expenses, reduces lead times, and allows for more agile production. 4. Design Optimization With additive manufacturing, intricate and complex geometries can be easily created, which may not be feasible with traditional methods. This design freedom allows for lightweight, part consolidation, and the integration of features, leading to optimized designs. Improved designs can result in reduced material usage, enhanced performance, and decreased assembly requirements, ultimately contributing to cost savings. 5. On-Demand Manufacturing Additive Manufacturing enables on-demand production, allowing organizations to manufacture parts as needed. This eliminates the need for large inventories, reduces warehousing costs, and minimizes the risk of obsolete or excess inventory. Companies can produce parts as they are required, resulting in more efficient use of resources and reduced storage expenses. 6. Customization and Personalization Additive manufacturing enables the production of customized products and tailored solutions. This customization capability allows organizations to meet specific customer requirements without the need for expensive retooling or reconfiguration. By catering to individual customer needs, organizations can enhance customer satisfaction, potentially leading to increased sales and revenue.
After playing a supporting role for 35+ years, Additive Manufacturing is poised to take center stage. With advancements in speed, materials, and Quality Management Software, AM is becoming a viable solution for numerous real-world production applications. As technical obstacles are overcome, manufacturers now face the responsibility of deepening their comprehension of these rapidly evolving technologies. They must develop the necessary skills, processes, and business models to unleash the full potential of additive manufacturing and showcase its brilliance in the industrial realm.
About Bluestreak™:
Bluestreak™ is a fully integrated Quality Management System (QMS) and a powerful Manufacturing Execution System (MES), designed for the manufacturing environment and service-based manufacturing companies ( metal-treating/powder-coating, plating, heat-treating, forging, and metal-finishing), businesses that receive customers’ parts, perform a process (service) on them, and send those parts back to the customer). Companies need MES software tailored to specific functionality and workflow needs such as industry-specific specifications management, intuitive scheduling control for both staff and machinery maintenance, and the ability to manage work orders and track real-time data. If different work centers on the production floor aren’t “speaking” to each other via the MES, the data loses value and becomes disjointed or lost in disparate silos.
Bluestreak | Bright AM™ is a QMS + MES software solution specifically designed to manage and optimize the unique requirements of Additive Manufacturing’s production of parts and powder inventory usage.
Comentários