Five Mistakes Profitable Manufacturers Avoid at All Costs
- Ron Beltz
- Feb 21
- 5 min read
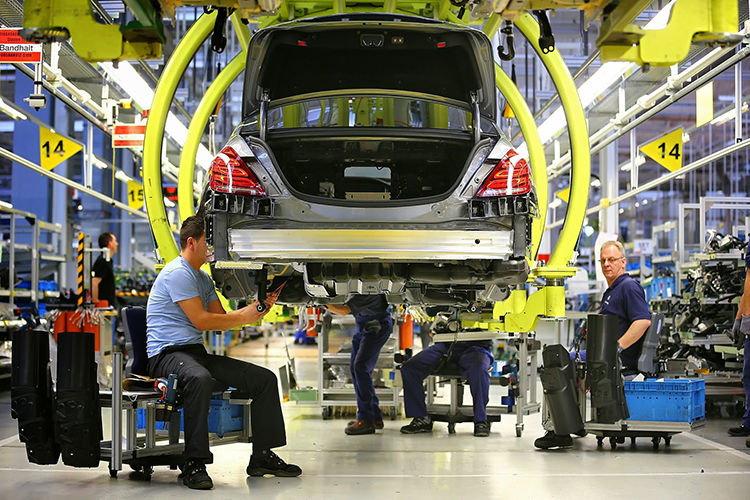
Bluestreak™ Reading Time: 5 minutes
Five Mistakes Profitable Manufacturers Avoid at All Costs
Key Points
Manual processes act like anchors in your business
Why paper-based tracking creates quality control nightmares.
How outdated data leads to production delays, scrap, and rework.
How siloed operations create inefficiencies, miscommunication, and increased costs.
The role of standardized work instructions and automated workflows in improving efficiency.
Running a high-performing manufacturing operation requires more than just efficiency—it demands precision, consistency, and smart decision-making at every turn. For manufacturers, delivering quality products on time, every time—often under tight deadlines—is non-negotiable.
But success isn’t just about what you do; it’s also about what you avoid. The most successful manufacturers recognize what slows them down, compromises quality, or disrupts workflow—and they eliminate it.
Here are 5 things top-performing manufacturers make a point NOT to do. How many are you avoiding?

ONE
MANUAL PROCESSES ACT LIKE ANCHORS IN YOUR BUSINESS Think of manual processes as anchors in your manufacturing operation—slowing down production, increasing errors, and adding unnecessary costs. Whether in the front office or on the shop floor, outdated workflows waste time, drive up labor costs, and create avoidable bottlenecks.
What’s the real impact of manual processes? Front Office: Lost paperwork, misfiled customer orders, and slow work order entry lead to costly delays and frustrated customers. Production Floor: Manually tracking job progress can cause scheduling conflicts, inefficiencies, and rework due to miscommunication.
Not long ago, manufacturers relied on spreadsheets, whiteboards, and paper trails just to keep things moving. But today, automation transforms these challenges into competitive advantages.
Faster Work Order Processing – Automated systems reduce job setup time, so production starts sooner.
Error Reduction – Digital job tracking ensures work is done to spec, reducing rework and scrap.
Real-Time Visibility – Instantly access job status, material availability, and quality control data from anywhere.
Lower Labor Costs – Eliminate repetitive manual tasks so your team can focus on value-added work.

TWO
USE PAPER ON THE SHOP FLOOR Relying on paper-based tracking in manufacturing isn’t just outdated—it’s a quality control nightmare. Paper gets lost, damaged, or misfiled, making it nearly impossible to maintain accurate records. Real-time visibility vanishes when work orders, inspection reports, and job travelers exist only in hard copies. This leads to missed defects, undocumented process deviations, and compliance gaps—all of which put customer satisfaction, audits, and profitability at risk. Why Paper Fails in Manufacturing:
No Real-Time Updates – Paper can’t tell you if a job is stalled or a spec changed mid-production.
Increased Errors – Handwritten notes lead to misinterpretation and costly mistakes.
Audit Headaches – Paper trails disappear, leaving you scrambling when auditors demand proof of process adherence.
Poor Traceability – If a defect is found, tracing it back through paper logs is slow, painful, and unreliable.
Wasted Time & Resources – Searching for missing documents, correcting errors, and managing paper stacks drains efficiency.

THREE
MAKE DECISIONS BASED ON OLD DATA
Making manufacturing decisions based on outdated data is like navigating with last week’s weather forecast—it’s unreliable, inefficient, and can be costly.
How Does This Happen?
Manual Data Collection – If job status, inventory levels, or equipment performance are tracked on spreadsheets or paper, updates lag behind reality.
Disconnected Systems – When ERP, QMS, and MES platforms aren’t integrated, production teams rely on old reports that don’t reflect current conditions.
Batch Data Entry – When data is entered only at the end of a shift or day, managers make critical decisions based on yesterday’s problems—not today’s.
The Risks of Using Old Data:
Production Delays – Scheduling based on old inventory data can lead to material shortages or bottlenecks.
Increased Scrap & Rework – Quality issues may go unnoticed until it’s too late, causing defective parts to move further into production.
Inefficient Resource Allocation – Outdated job tracking can result in underutilized machines or labor assigned to unnecessary tasks.
Compliance Failures – Relying on old inspection data in regulated industries can jeopardize certifications and customer trust.
Missed Cost Savings – Without real-time insight into machine performance, preventable downtime, and maintenance issues go unnoticed.

FOUR
DEPARTMENTS WORK IN SEPARATE SILOS
Why Working in Silos is a Recipe for Inefficiency
For production facilities and manufacturers, working in silos is one of the most significant barriers to efficiency, profitability, and overall business success. Siloed operations—where different departments, teams, or systems operate independently—create information gaps, slow decision-making, and introduce costly inefficiencies that impact quality, compliance, and customer satisfaction.
When departments such as quality control, production, maintenance, and logistics each use their disconnected systems or rely on manual communication, problems compound. A lack of real-time data exchange means that defects or process deviations may not be detected until it’s too late, leading to increased rework, scrap, or product recalls.
In contrast, an integrated Quality Management System like Bluestreak QMS + MES™ ensures that every department, from quality assurance to production and maintenance, works from the same set of real-time data. This synchronization eliminates redundant data entry, minimizes communication gaps, and enables faster decision-making, ensuring compliance with regulations.
Here's a quick list of top reasons siloed operations hurt manufacturers:
Delayed Decision-Making & Response Time
Inconsistent & Inaccurate Data
Higher Rework & Scrap Costs
Regulatory & Compliance Risks
Customer Dissatisfaction & Lost Business

FIVE
ALLOWING INCONSISTENT WORKFLOWS ACROSS DEPARTMENTS
One of the most common but highly damaging mistakes manufacturers make is operating without standardized workflows across different departments. When processes vary from one shift to another, or between production, quality control, and maintenance teams, the result is inconsistent product quality, increased errors, rework, and compliance risks.
How This Mistake Impacts Manufacturing
Quality Variability – If different operators follow slightly different procedures, product quality can fluctuate, leading to defects, scrap, and customer dissatisfaction.
Inefficient Troubleshooting – Without consistent, documented workflows, identifying and addressing production issues becomes time-consuming and error-prone.
Compliance Risks – Regulatory audits (e.g., ISO 9001, AS9100, ITAR) require evidence of standardized processes. Lack of workflow consistency makes it difficult to demonstrate repeatability and control.
Higher Training Costs – Without clear, standardized instructions, onboarding new employees or transitioning workers between roles becomes costly and inefficient.
Missed Continuous Improvement Opportunities – Without standardized workflows, manufacturers lack the baseline data needed for process optimization and lean manufacturing efforts.
Are You Avoiding These Costly Mistakes—Or Are They Holding You Back?
Avoiding these five critical mistakes isn't just about efficiency—it’s about survival. The most profitable manufacturers aren’t just the ones who produce the highest volume or run the fastest lines; they’re the ones who operate smarter, with precision, agility, and full operational visibility.
So, take a step back and ask yourself:
Are your workflows truly standardized, or do hidden inefficiencies lead to costly rework?
Do you have real-time visibility into production, or are you making decisions based on old data?
Is your team working together seamlessly, or are disconnected departments slowing you down?
Are you still relying on outdated paper-based tracking, risking compliance failures and lost productivity?
If any of these challenges sound familiar, you don’t have to accept them as the cost of doing business. Bluestreak QMS + MES™ is built to eliminate these bottlenecks—helping you streamline operations, enhance compliance, and drive profitability with data-driven precision.
Contact Bluestreak™ today to talk about how we can position your company on a more profitable, more agile, and more compliant path to success!
About Bluestreak™:
Bluestreak™ is a fully integrated Quality Management System (QMS) and Manufacturing Execution System (MES) designed for the manufacturing environment and service-based manufacturing companies (metal-treating/powder-coating, plating, heat-treating, forging, and metal-finishing), businesses that receive customers’ parts, perform a process (service) on them, and send those parts back to the customer). Companies need MES software tailored to specific functionality and workflow needs, such as industry-specific specifications management, intuitive scheduling control for staff and machinery maintenance, and the ability to manage work orders and track real-time data. If different work centers on the production floor aren’t “speaking” to each other via the MES, the data loses value and becomes disjointed or lost in disparate silos.
Bluestreak | Bright AM™ is a QMS + MES software solution specifically designed to manage and optimize the unique requirements of Additive Manufacturing’s production of parts and powder inventory genealogy usage.
コメント