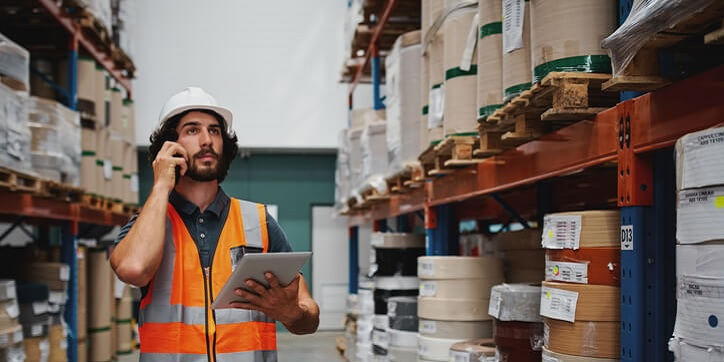
Bright AM Reading Time: 3 minutes
Struggles of Tracking Production
Additive Manufacturing (AM) is creating amazing results across a spectrum of industries and professions. A NASCAR team used AM for parts for wind-tunnel testing and reduced their costs by 89%. A turbine manufacturer printed wax mold patterns shaved 152 hours in processing time. NASA redesigned engine fuel injectors and was able to reduce 115 subcomponents into just two.
The potential use cases for Additive Manufacturing continue to grow.
Yet, many manufacturers still struggle with basic things, such as tracking production for clients. For most service-based manufacturers, production tracking is a manual process. It takes time and inhibits scalability. Customer queries create “busy work” for manufacturers because they often have to stop the process to provide accurate reporting.
The Most Common Struggles of Tracking Production
The most common struggle with tracking production is the manual workflow. There’s no easy way to track every part at every point in the production pathway. A disjointed workflow stems from a lack of real-time data. This, in turn, makes tracking difficult and visibility nearly impossible.
It also impacts quality assurance. Without visibility into every step of the production, it’s easy for quality to slip. Without process control, the information needed may not be available to the operator who needs it. Without quality control, your AM costs can skyrocket and lead to unhappy customers.
Even if you’re using software to manage the process, it may not be the right software for the job. For example, some manufacturers are trying to adapt ERP or other platforms to the AM process. But it doesn’t create a seamless workflow and doesn’t work at scale. Because it’s not designed for Additive Manufacturing, it also doesn’t account for tracking individually produced parts.
With time-sensitive materials, such as in 3D printing for biomedical products, ERP doesn’t adequately track resource and material shelf-life. When the compounds used have expired, it can lead to brittle products, cracking, and discoloration.
What Creates Additive Manufacturing Tracking Issues
When looking at what creates the biggest tracking issues in AM, it almost always goes back to the same problem: a lack of adequate digital infrastructure to manage AM production.
Lack of centralized production planning/monitoring
Inability to track parts and projects during builds
Data sync between systems
No end-to-end tracking
Additive Manufacturing requires precision at every level. Spreadsheets don’t provide real-time data and are notorious for data-entry errors. Using software not designed for Additive Manufacturing tracking increases the amount of manual entry that you have to do, which can lead to user errors. Most likely, it means operators on the shop floor may not have access to the precise data that they need when they need it.
For example, let’s say that a nonconformity has been discovered. A CAPA process has uncovered the root cause and the adjustments that need to be made to stop the mistake from reoccurring. However, the operator continues to work off the work order because it hasn’t been updated. When you’re using software that isn’t designed for the manufacturing process, there can be information silos that lead to significant—and costly—errors.
How Bluestreak | Bright AM Helps Solves Tracking Problems in Additive Manufacturing
There’s an easy solution to all these tracking problems: Bluestreak | Bright AM is an extensible real-time MES/QMS built exclusively for Additive Manufacturing.
It eliminates common tracking problems by creating a complete end-to-end digital infrastructure to manage production. It also eliminates manual tracking and automates the audit trail for compliance. Every operator has the most current information, including CAPAs tied right to the work order.
Bluestreak | Bright AM provides real-time shop floor tracking, including individual parts. Additive Manufacturers can track or split parts from work order steps to optimize production. There’s built-in traceability for individual parts at every step in the production cycle.
Traceability is essential. Bluestreak | Bright AM allows manufacturers to track every step of a product’s journey through the shop. Each component of a part is tracked from supplier and manufacturing to the customer. There is real-time visibility of every production step of the Additive Manufacturing process, control of the build plate and platform, and dialed-in quality control processes, procedures, and specifications for each operator and client.
Bluestreak | Bright AM’s Customer Connector acts as a self-service resource for customers by giving them 24/7 access to order. The fact that customers can pull real-time order status, certifications, and work order history for their tracking cuts down on the busy work for your staff.
Better Tracking in Additive Manufacturing
With powerful quality control tools that drive quality management directly to individual operators on the production floor, Bluestreak | Bright AM has the built-in functionality that Additive Manufacturing demands and that other MES, QMS, ERP, and MRP systems lack.
That’s why Bluestreak | Bright AM is currently being used by some of the world’s largest Additive Manufacturing companies at their facilities to track the entire production process, from order entry to shipment of completed parts. It makes struggling to track production a thing of the past with completely connected, real-time tracking for Additive Manufacturers.
Bluestreak | Bright AM is designed exclusively for the Additive Manufacturing industry. Our best-of-class MES and QMS solutions bring quality control management to new levels. Contact Bluestreak | Bright AM today for a free demo!
Comments