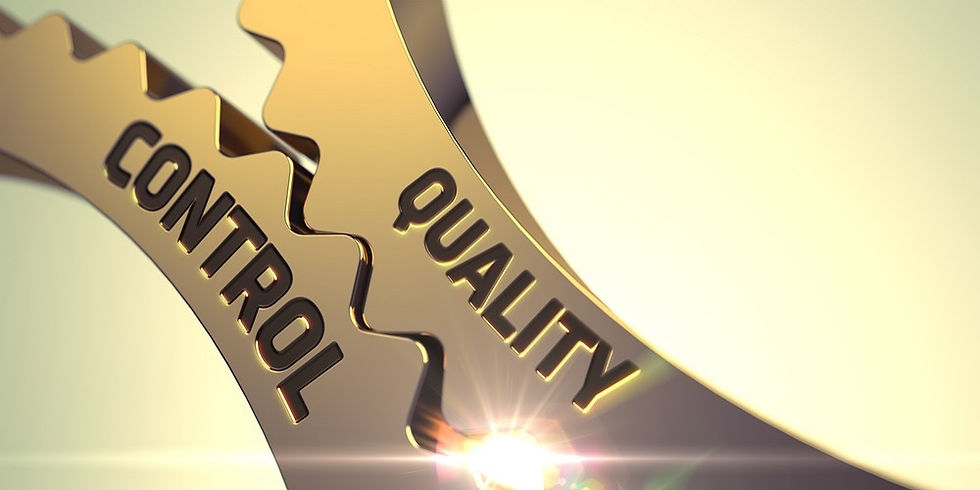
Bluestreak Reading Time: 3 minutes
Quality Control
No matter what causes poor quality and adds to your waste, scrap, and rework, the result is the same: it ties up resources, wastes time, and costs money. Reducing scrap and rework must be a priority in dealing with your quality control issues.
To drive consistent and sustainable yield, you must create a seamless workflow and understand the role that it plays in throughput, yield, energy, and quality control issues.
Here are common mistakes that lead to quality control issues.
1. Misunderstanding Product Specifications
Information silos in manufacturing are all too common and problematic. If specifications aren’t effectively communicated to everyone in the production chain, mistakes can happen. Paperwork can get lost or be outdated. Change orders may not be updated to the individual operator level. Corrective actions might be taken but fail to become part of the standard operating procedures.
Each of these avoidable quality control issues is solvable by creating an integrated end-to-end solution for production control.
2. Using Improper Tools
A common problem that will create quality control issues is when the wrong tools or improperly calibrated tools are used, including:
Machines that aren’t appropriate for the job
Machines that do not comply with project requirements
Machines that aren’t calibrated or maintained
Employees who are not qualified (certified) to operate a machine
Testing tools that are inadequate
3. Using Manual Processes
“Exceptio probat regulam in casibus non exceptis.” This Latin phrase translates to, “The exception confirms the rule in cases not excepted.” But you may be more familiar with the colloquialism: “lost in translation.” When you’re doing things manually, it’s easy for critical details to be lost in translation. Quality control issues are extremely difficult to manage when you’re doing things using a manual process.
4. Failing to Plan
Failing to adequately plan out your work or using institutional knowledge rather than facts and data to make decisions can lead to waste.
For example, nesting in metal stamping allows more than one part type per die by inserting smaller parts into areas that would otherwise be scrap. Stamping shops can utilize offal dies (recovery dies) to use scrap to produce other parts by stitching or fastening scrap into continuous strips. Many manufacturers fail to use nesting and recovery dies to minimize scrap.
Extra expenses add up when manufacturers do not have a formal scrap recycling program that can reuse scrap or sell it if it cannot be reused.
5. Failing to Test
Companies that effectively reduce their scrap involve everyone in the production chain to evaluate processes. Once potential solutions are identified, Multivariate Testing (MVT) is used to measure the effectiveness of possible solutions and how changes interact with each other and impact the outcomes.
How to Tell If Your Quality Control Plan Is Failing
Unacceptable levels of scrap and rework maybe two of the most obvious signs, but there are other warning signs that you should look for that indicate that your quality control plan needs work.
These include:
Missed deadlines and budgets
Higher than normal maintenance and/or support costs
Warranty repairs for defects
Failed audits
Customer complaints
Failure to meet customer demands
These are often symptoms of an inefficient quality control process. You’ll need to attach the root cause to change things. Don’t just mask the symptoms. When the quality control plan is flawed, your operation pays the price.
Practice Proactive Quality Control
A quality control plan helps you manage the manufacturing process and sets the stage for continuous improvement. If you wait to react until problems become obvious, it’s too late. Reducing quality control issues requires a proactive approach.
How Bluestreak Manages Quality Control
Bluestreak’s Integrated Quality Management System (QMS) ties quality control and quality assurance directly to individual work centers and processing steps on the production floor. An all-in-one inclusive database with no separate silos of disjointed data makes sure everyone has the latest documentation at all times. Real-time documentation is the key to consistency and repeatability and the underpinning for a quality control plan.
Conclusion
Avoiding quality control issues in manufacturing requires a proactive approach. Look for the warning signs early, and take steps to make changes before they grow into bigger problems.
It’s essential to look at quality control issues holistically. Examine the entire production process from start to finish, analyzing each step along the way. When you’re doing things manually on spreadsheets or utilizing software adapted from another industry, this can be extremely challenging. That’s because using the wrong software, i.e., ERP/MRP systems where the primary focus is inventory management typically requires expensive customizations to adequately handle service-based workflow requirements.
Bluestreak’s QMS is designed exclusively for the manufacturing industry to drive quality control management from the front office directly to the production floor. Contact Bluestreak for a quote, and start on your path to solving quality control issues.
Comments