top of page
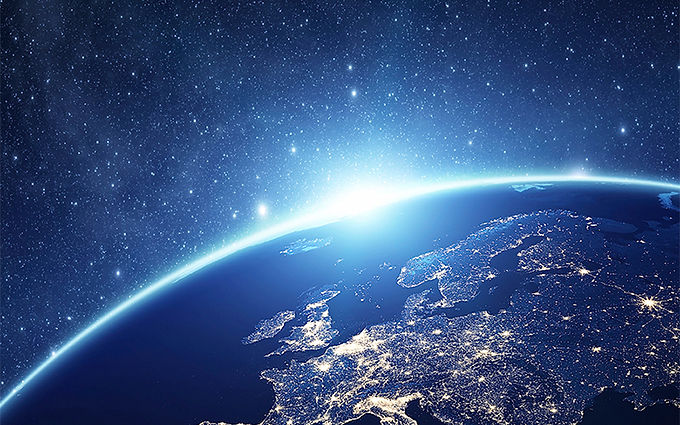

Click below to request a demo video.
“The interactive and multifaceted business systems that have been implemented as part of the Bluestreak software are, in my experience, far and away one of the best application for the control and management of a Quality Management System. As auditors, we get to see all sorts of applications for the control of activities, documentation, and records. The Bluestreak approach that is being used is definitely a best practice. I found that the system supported the integration and implementation of the controls necessary for a solid QMS in ways that are easy to understand and appeared to be easy to use. I have no doubt that this system will be a real plus for the team going forward.”
- See how to generate unique serial numbers per your pre-defined formats
- Learn how to optimize the routing of work on the production floor
- View our dynamic real-time tracking of out-of-sequence operating steps
- Hear about multiple, mutually exclusive Part-build Process routes
- See how you can disposition Part Nonconformance “on-the-fly”
- Learn how to Print multiple or batched Parts on the same Build Plate
- Learn how to reduce your rework and scrap by at least 25%
- Find out how to make your auditors love your manufacturing business
- See how to meet your documentation requirements automatically
- Discover the advantages of having your company data in one database
- See how easy it is to generate a quote and initiate a work order
- Learn how to monitor all your work-in-progress, at every stage
- Find out how to manage user viewing restrictions and permissions
- View our time-tested online training video library, available 24x7x365
- Hear about our step-by-step implementation and training process
- See how any user can easily enter a Help Request
- Manage your business with real-time key performance indicators (KPIs)
- Connect quality management initiatives directly to the production floor
- Learn how to tie equipment maintenance directly to activities
- See how to collect quality-related processing data in real-time
- View our integrated quality management system with document control
- & more!
CONTACT US NOW
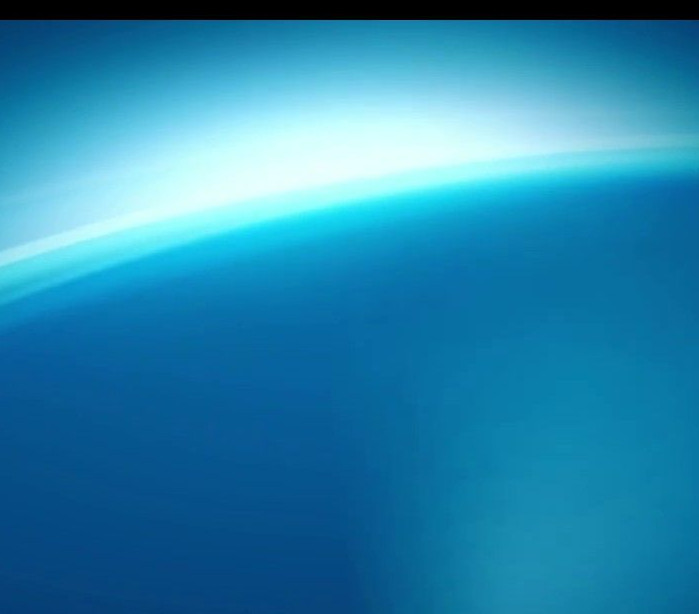
bottom of page